November 28, 2024 – White Masterbatch: The Unsung Hero of Plastic Manufacturing
White masterbatch, a plastic additive that may seem unfamiliar to many yet is omnipresent in our daily lives, plays a pivotal role in the plastics industry. From injection molding and blow molding to household appliances, toys, packaging materials, and automotive construction, white masterbatch stands out with its bright color, high coloring strength, and excellent dispersion properties.
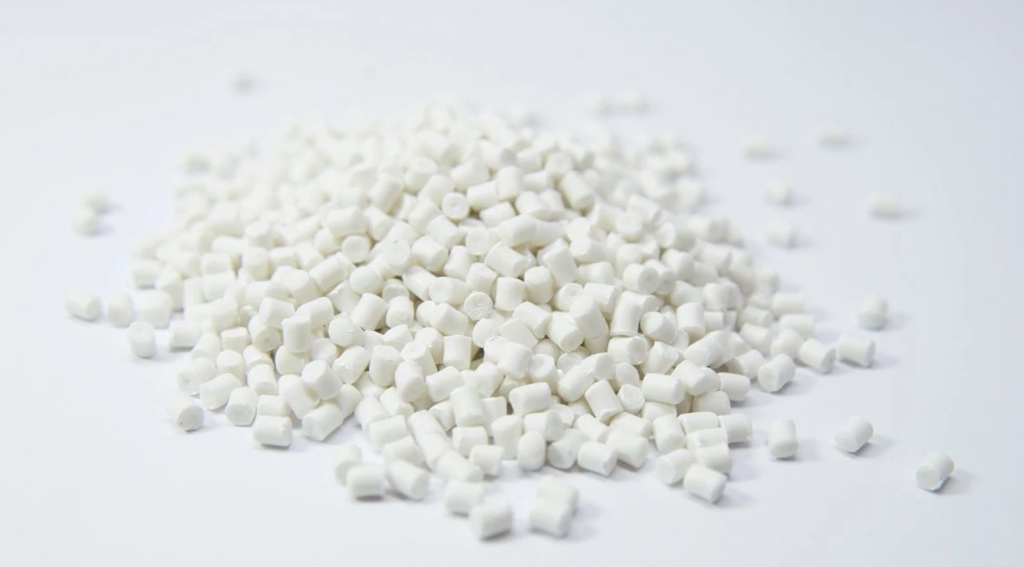
But how can one discern the quality of white masterbatch? The answer lies in a few key technical indicators. Firstly, it must meet standards for migration resistance and heat resistance, ensuring that the masterbatch remains stable during processing. Secondly, a low moisture content and minimal color difference guarantee product consistency and stability. Moreover, an appropriate melting temperature and good dispersion within the plastic are crucial to avoid any color spots or stripes. Lastly, a uniform appearance and consistent color are also vital signs of quality.
When using white masterbatch, several precautions should be taken. To minimize color variation in the final fiber, it is essential to dilute the masterbatch and control the mixing ratio. The method of incorporation is equally important, requiring uniform dispersion in polypropylene chips before spinning to maintain product quality. Additionally, selecting the right grade of white masterbatch based on the denier of the fiber being spun is crucial. To avoid quality variations due to differences in light and heat stability of the pigments, choosing masterbatches with similar stability levels is recommended.
Interestingly, opting for white masterbatch from a single manufacturer not only ensures consistency in product quality but also reduces costs. Furthermore, selecting the appropriate grade of white masterbatch based on the desired fiber quality is vital. Coarser fibers require a lower concentration compared to finer ones, with the application ratio being directly proportional to the square root of the fiber denier—a detail that warrants careful attention during operation.