March 31, 2025 – Unveiling the Secrets of Automotive Masking Film Blowing Process: Material Selection and Operation are Key!
In the realm of automotive maintenance, the blowing process of automotive masking films is truly an art form, directly impacting the masking effectiveness and user experience. So, how do we select the appropriate blowing materials and ensure correct operation? This article will provide detailed insights.
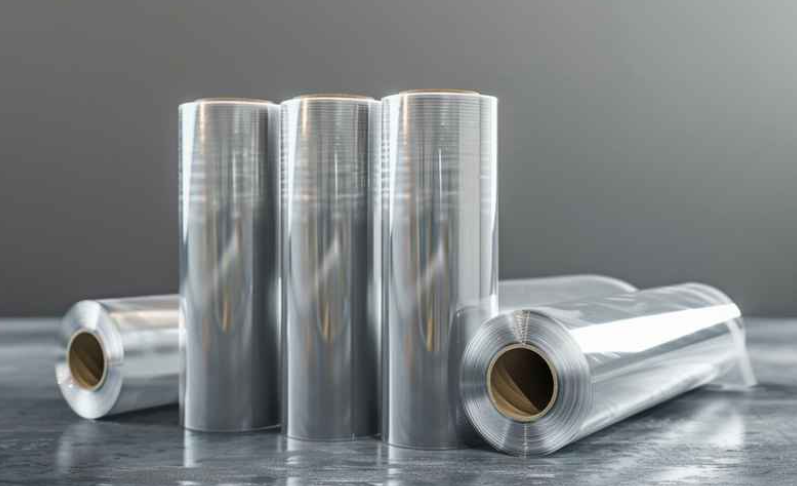
I. A Comparative Look at Automotive Masking Film Blowing Materials
There is a diverse range of materials used for blowing automotive masking films, each with its own unique advantages. PVC films are weather-resistant and flexible, making them suitable for everyday use and rainy conditions. Aluminum-based films offer scratch resistance and corrosion resistance, albeit at a higher cost, but they are aesthetically pleasing and durable, making them the preferred choice for interior applications. PP films are impact-resistant and anti-aging, with lower costs but slightly inferior weather resistance. PU films combine anti-aging and scratch-resistant properties, suitable for high-impact scenarios. When choosing, it’s essential to consider specific requirements.
II. A Comprehensive Analysis of Automotive Masking Film Blowing Process
To blow automotive masking films, one must first prepare the materials, ensuring their surfaces are clean and free of scratches. Next, heat the materials to the appropriate temperature. During the blowing process, it’s crucial to blow air evenly and control the airflow to prevent material deformation or damage. After blowing, cut the film to the appropriate size and secure it with strong adhesive or hot-melt glue.
According to insights from the Color Masterbatch Industry Network, temperature control is paramount during the blowing process, as too high or too low temperatures can affect the blowing results. Additionally, the blowing method must be precise, with even and slow airflow to avoid localized overheating or excessive force.
III. Stringent Quality Control Standards
After the automotive masking film is blown, quality control cannot be overlooked. Surface smoothness, dimensional accuracy, weather resistance, and tensile strength must all be thoroughly tested to ensure the film meets design requirements and performs reliably in practical applications.
IV. Key Considerations to Keep in Mind
When selecting blowing materials, consider the application scenario and requirements. During the blowing process, strictly control the temperature and ensure even airflow. After blowing, conduct comprehensive quality testing. Only by adhering to these guidelines can we ensure optimal blowing results for automotive masking films, providing better protection and maintenance for vehicles.
In summary, although the blowing process of automotive masking films is not overly complex, each step requires careful attention. Through proper material selection, scientific process operation, and rigorous quality control, we can create high-quality automotive masking films, adding a touch of elegance to vehicles.