May 15, 2025 – The fundamental disparity between thermosetting plastics and thermoplastics lies in their cross-linking mechanisms. Thermosetting plastics, owing to the cross-linking process, inherently exhibit superior mechanical properties, elevated heat resistance, and remarkable dimensional stability. These materials are predominantly classified as engineering plastics and, due to cross-linking, often possess an amorphous structural configuration.
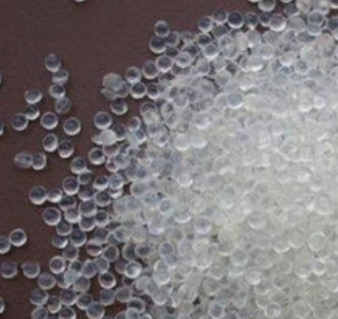
Prior to molding, both thermosetting and thermoplastic polymers share a similar chain-like molecular structure. However, during the molding process, thermosetting plastics undergo a polymerization reaction triggered by heat or chemicals, gradually forming a cross-linked structure. Upon completion of the reaction, the polymer molecules interlock into a three-dimensional network, effectively preventing relative sliding between molecular chains. This transformation results in a solid material that neither melts nor dissolves.
As per insights from the Color Masterbatch Industry Network, without undergoing a decomposition reaction, subjecting thermosetting plastics to heat treatment does not allow them to resoften or undergo reprocessing. This characteristic can be aptly likened to a hard-boiled egg; once the yolk transitions from a liquid to a solid state, it cannot revert to its liquid form.
Thermosetting plastics are commonly available on the market as liquid monomer-polymer mixtures or partially polymerized molding compounds. In their uncured state, these materials are injected into molds and cured through heating or chemical catalysts, with or without applied pressure.
To further enhance the performance of thermosetting plastics, fillers or reinforcing materials such as minerals, lime, and glass fibers are frequently incorporated. These additives aid in controlling shrinkage, improving chemical resistance, enhancing shock absorption, and refining insulation and thermal barrier properties, while also contributing to cost reduction. The finer the mesh structure of thermosetting plastics, the better their heat and chemical resistance typically become. Epoxy resins and phenolic resins are among the prevalent types of thermosetting plastics, playing a pivotal role in the manufacturing of products such as integrated circuits (ICs).