October 10, 2024 – Ultra-Fine Calcium Carbonate: A Versatile Ingredient in the Chemical Industry with Distinct Technical Specifications
Ultra-fine calcium carbonate (UFCC) holds a pivotal position in the chemical industry, with its technical specifications such as particle size, specific surface area, crystal morphology, and oil absorption value exerting profound impacts on product performance. These specifications not only dictate the fundamental characteristics of UFCC but also play a crucial role in its trend towards specialization, serialization, diversification, and functionalization.
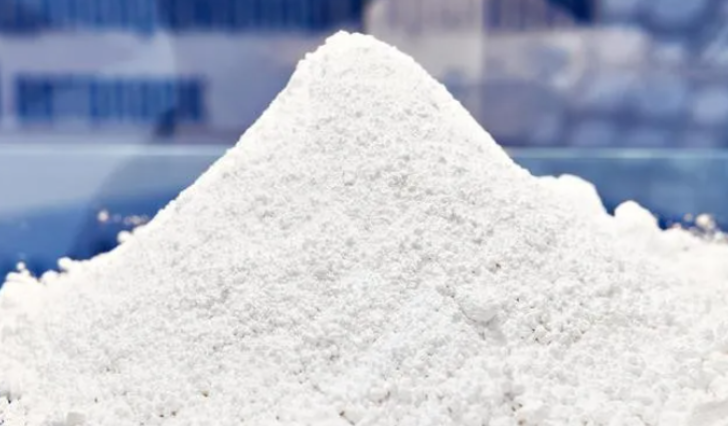
In the preparation of UFCC, particle size and specific surface area are two closely intertwined parameters. Ensuring an average particle size of 0.02 to 0.1 micrometers for primary particles is not only a foundational requirement but also a prerequisite for its widespread application. However, merely achieving this particle size is insufficient. If surface treatment and dispersion technologies lag, primary particles tend to aggregate into larger secondary particles, compromising the product’s actual performance. Therefore, a combination of transmission electron microscopy observation and specific surface area measurement is essential for a comprehensive and scientific assessment of UFCC’s micro-fineness, crystal morphology, and dispersion state.
Crystal morphology, another vital technical specification of UFCC, significantly influences product performance. Different applications demand distinct crystal morphologies to meet specific performance requirements. For instance, UFCC used in plastics prefers simple crystal structures, small aggregate volumes, and low oil absorption values, making cubic or spherical morphologies more suitable. In contrast, UFCC for rubber applications requires chain-like crystal morphologies to enhance its reinforcing effects in rubber. For ink applications, cubic crystal morphologies are favored to improve ink gloss and flowability.
The oil absorption value, a key indicator of UFCC’s application performance, is particularly crucial in plastics, coatings, and inks. Excessive oil absorption not only consumes significant amounts of plasticizers or increases viscosity but also affects product processing and usage effectiveness. Therefore, during UFCC preparation, factors such as particle size, dispersion performance, and specific surface area must be comprehensively considered to reduce oil absorption and enhance product performance.
Furthermore, the main content of UFCC, another critical specification, needs to be controlled within an appropriate range. While UFCC primarily serves as a functional filler with minimal impact on the chemical properties of the filled material, its physical properties are closely related to the main content. During preparation, certain control agents, dispersants, and surface treatment agents are often added to obtain UFCC with different crystal morphologies, good dispersion performance, and excellent activation properties. These intentionally added “impurities” typically have no adverse effects on UFCC’s application performance and can even be beneficial. However, harmful elements such as iron and manganese must be strictly controlled to avoid adverse impacts on product performance and resin aging.
According to insights from the Color Masterbatch Industry Network, the key development directions for UFCC are specialization, serialization, diversification, and functionalization. Different applications of UFCC require tailored and distinctive requirements for particle size, crystal shape, specific surface area, oil absorption value, and main content. This approach better meets the needs of various industries and users, driving the continuous development and innovation of the UFCC industry. Therefore, specialized varieties of UFCC for different applications cannot be simply evaluated using uniform standards.