December 31, 2024 – Yichang Hengdali Recycling Project Marks Significant Milestone in Waste Tire Utilization
Yichang Hengdali Renewable Resources Co., Ltd. has recently achieved a crucial breakthrough in its major waste tire recycling and reuse project invested in Yidu Chemical Industry Park. With a total investment of RMB 326 million, four production lines have now completed debugging and are poised for official launch. The project, which commenced construction in July 2023, has garnered significant industry attention.
According to AsiaMB’s sources, the factory is built to precision chemical standards, incorporating advanced DCS control systems that enable highly intelligent and standardized production processes. This innovative project utilizes cutting-edge production line technology to convert waste tires into high-value steel wires, heavy oil, and carbon black. The extracted high-purity steel wires find wide applications in tire manufacturing, steel casting, and other sectors. Heavy oil serves as a vital fuel for ocean-going vessels and chemical enterprises, while carbon black is used in combustion promoters, color masterbatches, and tire production, maximizing resource recycling and value.
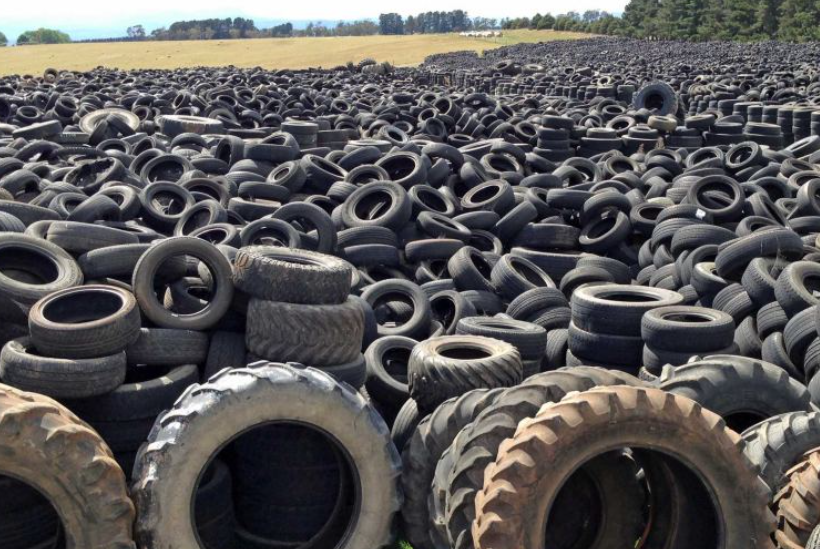
In the shredding workshop, company head Wang Donghai demonstrated the waste tire processing procedure to reporters. He highlighted that each waste tire contains approximately 8 kilograms of steel wire, which is meticulously extracted by wire rolling machines and stacked in bundles. The current market price for steel wire stands at over RMB 2,000 per ton. After steel wire removal, tire fragments are sent to rubber crushing equipment for grinding, followed by entry into a high-temperature pyrolysis furnace operating at 380°C to 400°C. Through physical evaporation, heavy oil and carbon black are separated. Carbon black is then pneumatically conveyed to the deep processing area for further treatment, while incompletely processed tire fragments are re-ingested into the equipment for cyclic grinding and steel wire recovery.
Wang Donghai emphasized that this comprehensive waste tire utilization project completely颠覆s the traditional stereotype of smoke-belching tire processing. The entire production process adopts a flameless design, with pyrolysis furnace heating regulated by a frequency conversion hot air furnace for precise temperature control. Furthermore, gases generated in the pyrolysis furnace are recycled to continuously heat the furnace, forming an efficient energy cycle. Post-combustion exhaust undergoes professional environmental protection equipment for denitrification and desulfurization treatment, equipped with online monitoring devices to ensure emission compliance, highlighting the project’s commitment to environmental protection.
Notably, the municipal development and reform commission has officially issued a subsidy document for the “two new” national debt project funds, providing corresponding subsidies based on the actual completion ratio of the project’s investment. Upon full completion and commissioning, the project is expected to process 100,000 tons of waste tires annually, with an estimated annual output value ranging from RMB 210 million to RMB 250 million. This not only offers an innovative solution for waste tire recycling but also actively contributes to promoting a green economy and sustainable development.