February 23, 2025 – Mineral powder materials play a vital role in the plastics industry, encompassing a wide range such as calcium carbonate, talc, and kaolin. These materials are extensively used in plastic products with the primary objectives of filling, performance enhancement, and cost reduction.
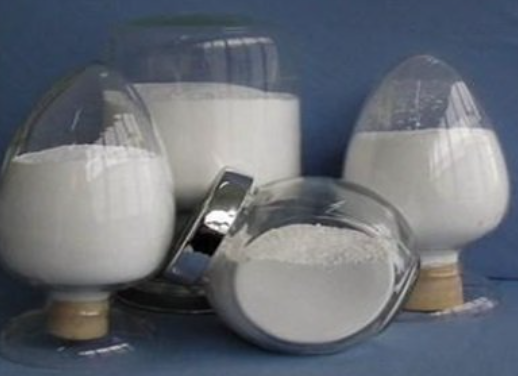
The selection of mineral fillers is not arbitrary; they significantly impact the properties of plastic products. Factors such as the geometric shape, particle size and distribution, surface characteristics, density, hardness, and whiteness of the fillers are crucial in determining the final performance of plastic products. For instance, fibrous fillers can markedly boost the mechanical strength of the products, while spherical fillers facilitate molding processes but may compromise some mechanical strength.
According to AsiaMB’s insights, the smaller the particle size of the fillers and the more uniform their dispersion, the better the mechanical properties of the plastics tend to be. However, this also increases the complexity and cost of the processing. Additionally, the surface roughness and free energy of the filler particles have a significant influence on the plastic manufacturing process. To reduce particle aggregation and avoid uneven stress distribution in the products, it is often necessary to lower the surface free energy of the filler particles during actual production.
Beyond these characteristics, the specific surface area, density, hardness, color, oil absorption value, optical properties, electrical conductivity, and chemical composition of the fillers also exert noticeable effects on plastic products. For example, high-hardness fillers can enhance the wear resistance of the products but may also wear down processing equipment. Fillers with high whiteness can better maintain the color of the matrix, while those with low oil absorption values can reduce the amount of plasticizers needed, improving the processability of the material.
Notably, inorganic mineral fillers exhibit thermochemical effects. As most inorganic mineral fillers are non-combustible, their addition to polymer matrices can reduce the amount of combustible material and delay the combustion of the matrix. Particularly, fillers like magnesium hydroxide and aluminum hydroxide, upon decomposition, generate steam and metal oxides that exhibit excellent flame-retardant properties without producing toxic smoke, making them preferred choices for environmentally friendly flame-retardant fillers.
In summary, inorganic nonmetallic mineral fillers serve multiple purposes in polymer composites, including filling, reinforcement, and imparting new functionalities. However, due to the poor compatibility between inorganic nonmetallic mineral fillers and organic polymers, modifying them to enhance their compatibility with organic polymers is key to avoiding stress dispersion issues caused by direct addition.