October 29, 2024 – Vibration Screens: The Unsung Heroes of Modified Plastics Production
In the production process of modified plastics, vibration screens stand as pivotal sorting and classifying equipment, playing a crucial role thanks to their unique vibration principle. This principle effectively promotes material layering and screening, achieving precise sorting and classification. However, maintaining stable operation of vibration screens in practical applications is not a trivial task. Their performance is influenced by various factors, and any malfunction can not only impair production efficiency but also significantly degrade the quality of finished products.
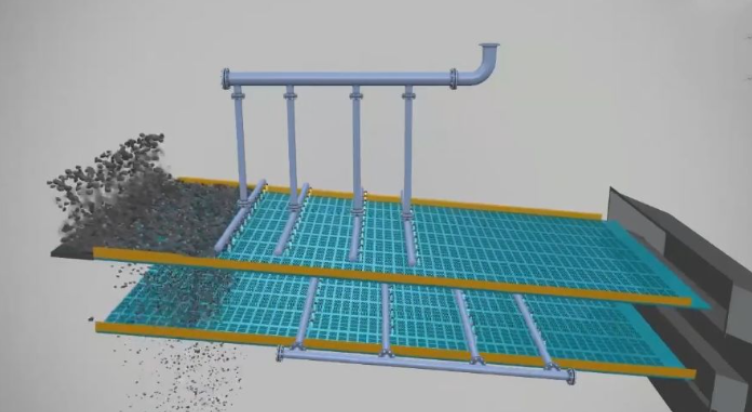
Recently, AsiaMB encountered a production issue at a blending factory stemming from improper use of vibration screens. At this factory, the waste rate of pelletized products after passing through the vibration screens was alarmingly higher than the rate of quality products. This abnormal phenomenon caught AsiaMB’s attention. Upon close inspection, it was discovered that one corner of the vibration screen was in contact with the pelletizing machine. The interaction between the two during vibration compromised the pelletizing and screening effects. Fortunately, the factory promptly identified the issue and separated the vibration screen from the pelletizing machine, restoring normal screening performance. However, the waste already incurred was regrettable.
AsiaMB understands that vibration screens can suffer from various faults, including poor screening quality, non-compliance with operational specifications, and severe wear and tear of components. These faults can be caused by mechanical issues, electrical problems, or improper human operation. To ensure stable operation of vibration screens and improve production efficiency, timely troubleshooting and prevention measures are necessary.
Addressing poor screening quality requires a multi-faceted approach, considering feed material properties, equipment factors, and operational factors. For instance, when screen holes are blocked, they should be promptly cleared, and the water spray volume and screen inclination angle should be adjusted. When screen holes are severely worn, worn-out holes should be repaired or the screen mesh replaced. Additionally, uneven feeding or excessive material thickness on the screen can affect screening effectiveness, necessitating adjustments to the feed chute width or other specific measures.
For issues of non-compliance with operational specifications, attention should be paid to key indicators such as screen speed, vibration force, and amplitude frequency. When faults like inability to start, excessively small amplitude, insufficient speed, or weak vibration force occur, one should first check for electrical system issues, such as motor damage or insufficient voltage. After eliminating electrical faults, mechanical aspects should be examined, including severe material accumulation on the screen surface, detachment of bolts on the coupling joint of the vibrator, or solidified lubricating grease, and timely measures should be taken.
Regarding severe wear and tear of components, regular inspections and replacements of worn-out parts are required. For instance, when pipes, beams, crossbeams, or screen frames are fractured, damaged components should be promptly replaced, and the rigidity and stability of related parts should be enhanced. Meanwhile, attention should be paid to abnormal sounds during screen operation, and issues like spring damage, bearing wear, loose bolts fixing the bearings, or untightened screen mesh should also be promptly addressed.
Lastly, to ensure long-term stable operation of vibration screens, enhanced routine maintenance is necessary. This includes optimizing screen design, ensuring manufacturing precision, correct installation and operation, regular overhauls and maintenance, and more. Only in this way can vibration screens maximize their effectiveness in the production process of modified plastics.