November 12, 2024 – Unveiling the Secrets of High-Temp Additives for Advanced Polymers
In the chemical industry, the application of high-temperature polymers is on the rise, yet common additives often fail to meet stability requirements in such extreme conditions. This has sparked an urgent need for specialized additives tailored to these polymers. Today, we delve into three crucial high-temp additives – antioxidants, flame retardants, and processing aids – the hidden heroes behind enhanced polymer performance.
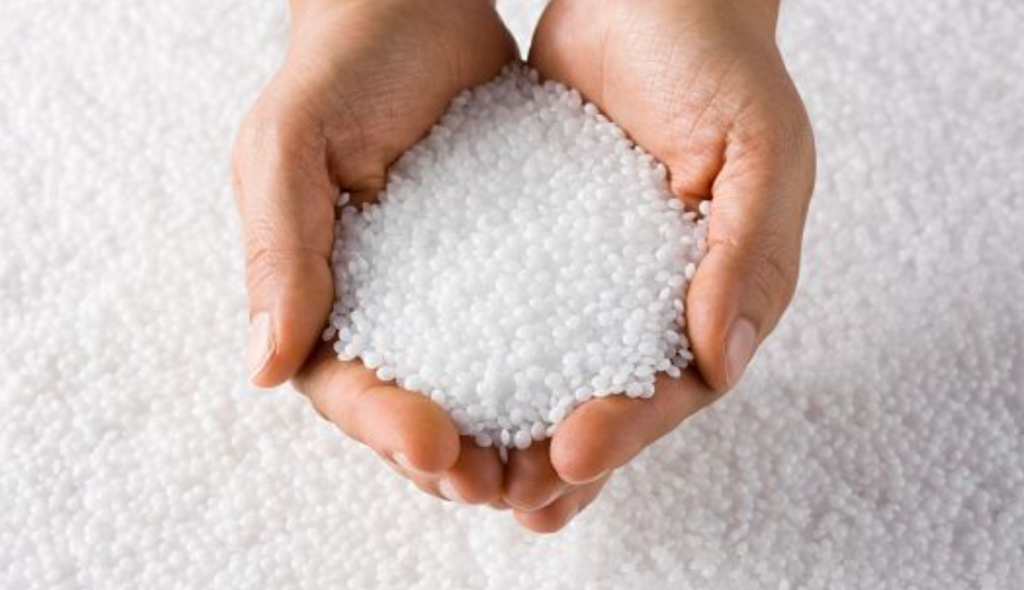
The rapid evolution of sectors like aerospace, automotive, and electronics has fueled the demand for high-performance components. These parts must withstand high temperatures while balancing thermal, mechanical, and electrical properties. To meet these stringent criteria, special high-temperature polymers have emerged, capable of maintaining stability at temperatures exceeding 250°C. However, these polymers aren’t infallible; they require specific additives to unlock their full potential.
So, how do we choose the right high-temp additives? According to industry experts, it primarily depends on the polymer type and application. Different additives bring unique benefits, and their strategic combination is key to creating valuable plastics that are both heat-resistant and advantageous in other ways.
Let’s start with flame retardants. Commonly used in high-temp polymers, options include brominated, chlorinated, phosphorus-based, and metal oxides. While brominated and chlorinated retardants are widespread, they pose health risks. Thus, halogen-free alternatives, particularly phosphorus-based and metal oxide retardants, are gaining traction. They’re not only environmentally friendly but also significantly boost polymer flame resistance.
Next up are antioxidants. High-temp polymers are prone to oxidative degradation during processing and use, and antioxidants provide the solution. Unlike hindered amine antioxidants used in low-temp processes, high-temp polymers require phosphites and hydroxyamines. These stabilize the polymer at high temperatures, minimizing discoloration and melt viscosity changes, thereby ensuring consistent product performance.
Lastly, processing aids play a vital role. During high-temp polymer processing, compatibility between the aid and polymer is crucial. To enhance this, researchers are incorporating chemical functional groups into fluoropolymers, enabling interaction with the base high-temp polymer. This reduces extruder backpressure and minimizes degradation, ultimately enhancing the mechanical properties of the final components.
In conclusion, as the application scope of high-temperature polymers expands, so do the demands on additive development. Only through continuous innovation and optimization can we meet the rigorous requirements of specific applications, allowing high-temp polymers to shine across various industries.