October 23, 2024 – Polyethylene (PE), a vital thermoplastic used across packaging, construction, electronics, and healthcare, sees its melting point as a crucial parameter in materials science, significantly influencing its application characteristics and processing conditions. With a melting point range roughly spanning from 105°C to 135°C, the exact value depends on the polymer’s molecular structure and density. High-density polyethylene (HDPE) boasts a higher melting point interval, approximately 130°C to 135°C, while low-density polyethylene (LDPE) features a lower range, between 105°C and 115°C. This disparity primarily stems from differences in molecular chain packing density and intermolecular forces.
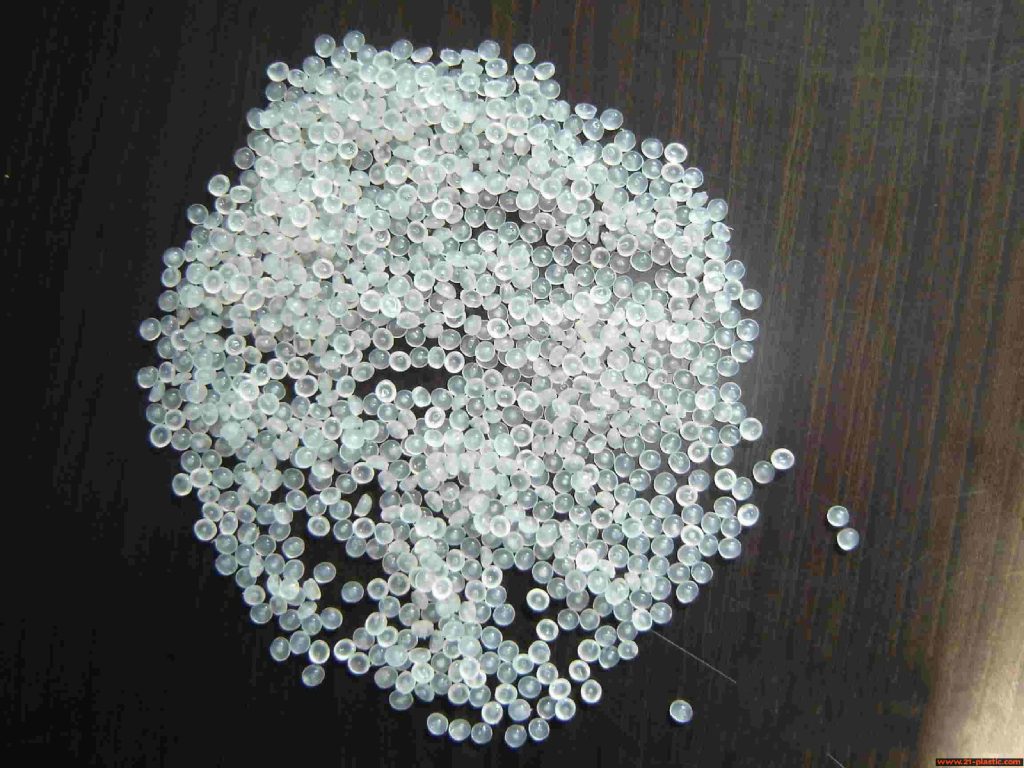
The melting point of PE directly correlates with its processing applications. During manufacturing processes like injection molding, the material must be heated above its melting point to achieve flow and facilitate mold filling. A precise understanding of the melting point helps optimize processing temperatures, enhancing production efficiency and product quality. Moreover, the melting point determines PE’s suitability for various environments. HDPE, with its heat resistance from a higher melting point, is ideal for high-temperature applications such as hot water pipes and food packaging. In contrast, LDPE, with a lower melting point and excellent flexibility, shines in films and flexible packaging.
According to insights from the Color Masterbatch Industry Network, PE’s melting point is also closely linked to its chemical stability. Under high temperatures, PE’s molecular chains may degrade, leading to performance deterioration. Therefore, when selecting materials, it’s essential to consider the alignment between the melting point and the intended use environment to ensure long-term stability and safety.
In summary, PE’s melting point stands as a pivotal indicator of its material properties, fundamentally dictating its processing methods and application scope. A thorough grasp of the melting point’s implications enables more precise material selection and application, catering to the diverse needs of various industries.