December 9, 2024 – In the plastic processing industry, the selection and application of colorants play a crucial role. Plastic coloring primarily relies on inorganic and organic pigments, which must possess a range of excellent properties, including high coloring strength and brightness, good transparency or opacity, superior dispersibility, weather resistance, thermal stability, chemical stability, electrical functionality, and environmental performance.
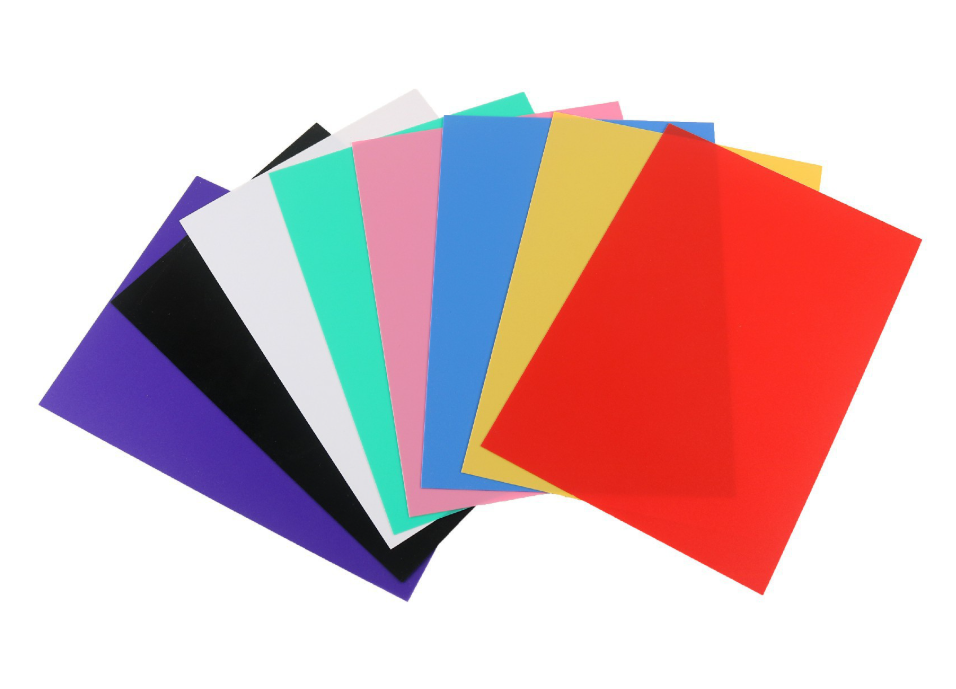
The coloring power is directly related to the amount of colorant used. Generally, as the particle size of the colorant decreases, its coloring power increases accordingly. Organic pigments often surpass inorganic pigments in terms of coloring power, especially when used in conjunction with white pigments, resulting in more pronounced coloring effects. Currently, the widespread application of organic pigments and ultrafine particle technology has opened up more possibilities for plastic coloring.
Dispersibility is a key factor influencing the coloring effect. To ensure uniform dispersion of pigments in polymers, high shear force processing is required to break down large aggregates into minute particles. According to Color Masterbatch Industry News, techniques such as pigment surface treatment can be employed to process them into practical forms like color masterbatches, thereby effectively improving dispersibility. Additionally, the addition of specific additives can further enhance the dispersion of colorants.
In terms of light and weather resistance, inorganic pigments typically exhibit better light stability. Among organic colorants, phthalocyanines and quinacridones also possess excellent lightfastness, comparable to inorganic pigments. Migration resistance is another important consideration, relating to the stability of colorants within polymers. Due to their heterogeneous dispersion, inorganic pigments are less prone to migration, while organic pigments may migrate due to differences in solubility. The ease of migration is closely related to the type of polymer and additives used.
Thermal stability is an indispensable performance indicator for plastic colorants. Most inorganic pigments can meet the high-temperature requirements of plastic processing, while organic colorants may fall short in this aspect. The chemical structure of different resins and plastics determines their processing temperatures, which in turn influence the choice of colorants. To ensure stable coloring effects, it is necessary to select appropriate colorants based on specific processing temperatures.
Regarding chemical stability, the impact of the plastic’s usage environment on the colorant must be considered. For example, chlorine-containing polymers like PVC may generate hydrogen chloride during decomposition, damaging the colorant. Therefore, when selecting colorants, special attention should be paid to their chemical resistance. Electrical performance is particularly important for plastics used as insulation or sheathing for wires and cables. Some colorants may reduce electrical insulation performance, often related to electrolyte residues on the pigment surface. Thus, careful selection is required.
With increasingly stringent environmental regulations, the toxicity of plastic colorants is also gaining attention. Many countries and regions have imposed clear restrictions on the use of heavy metal colorants and have set strict requirements for the use of aromatic amine dyes and organic pigments. Although China has made some progress in replacing toxic colorants, it still faces technical and cost challenges. In the future, the research and application of environmentally friendly colorants will become a significant trend in the industry’s development.