August 26, 2024 – Calcium Carbonate: A Pivotal Industrial Material with Stringent Quality Metrics Impacting Subsequent Product Performance
Calcium carbonate, a vital industrial raw material, exhibits quality technical indicators that significantly influence the performance of derivative products. Within the chemical industry, particularly in the production of modified masterbatches, there are rigorous requirements for various parameters of calcium carbonate.
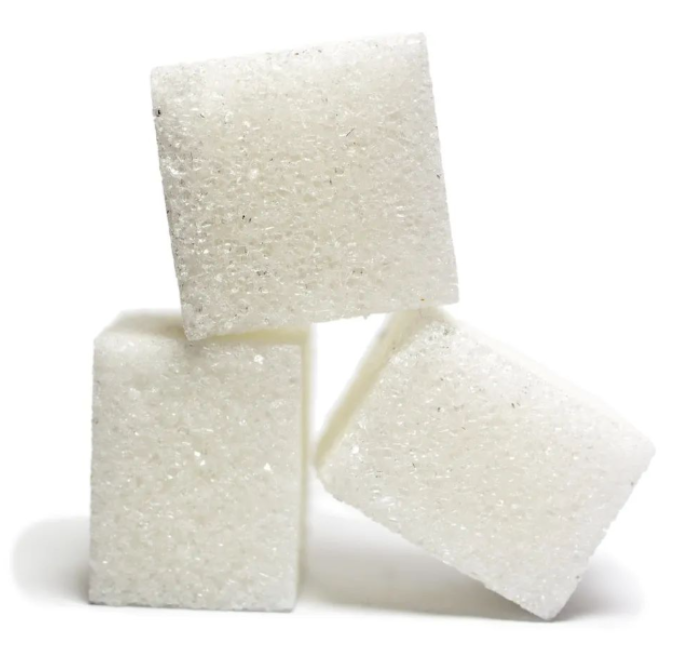
One of the crucial factors in assessing calcium carbonate’s quality is its calcium content. The production of modified masterbatches typically demands a calcium content exceeding 98%, as high calcium levels ensure more stable processing performance. Insufficient calcium content may lead to an increase in heavy metals and other non-metallic impurities, which not only affects the usage effectiveness of calcium carbonate but also poses potential adverse effects on processing techniques and product quality, potentially even harming processing equipment.
Furthermore, whiteness and color shade are essential indicators for evaluating calcium carbonate’s quality. Whiteness directly impacts the whiteness and colorability of modified masterbatches. Currently, the market requires a whiteness level of over 95% for 400-mesh calcium carbonate, with some high-quality mineral-processed calcium carbonate reaching whiteness levels of up to 97%. To enhance product whiteness, some manufacturers add fluorescent whitening agents. However, improper selection or excessive amounts of these agents may result in product decomposition, yellowing, poor dispersibility, or agglomeration. Notably, for plastic products involving hygiene safety and human contact, fluorescent whitening agents may cause irritation, necessitating cautious usage. Additionally, color shade, influenced by mineral structure and origin, directly correlates with the coloring, hue, and gloss of plastic products.
Moreover, moisture and volatile content are crucial quality control points. Calcium carbonate is prone to moisture absorption during processing, storage, and transportation. Excessive levels of these substances can adversely affect modified masterbatches and plastic products. Therefore, it is usually necessary to control moisture and volatile content at approximately 0.3%. In practical applications, if the moisture content in the product exceeds this standard, it may compromise product quality, leading to issues such as surface roughness, bubbling, burning, or decomposition. To effectively manage moisture content, a common method is to use high-speed mixers for heating and drying.
In the production and processing of calcium carbonate, particle size distribution is also a significant consideration. A narrower particle size distribution range indicates more stable material performance. For instance, 1250-mesh calcium carbonate should have a particle size of around 10 micrometers. If the particle size distribution is too wide, it may lead to problems such as rough product surfaces, further impacting processing performance and mechanical properties.
Additionally, the particle shape of calcium carbonate significantly influences the processing techniques of modified masterbatches and product quality. Particles of different shapes exert varying degrees of influence on melt flowability, coating crosslinking effects, and the physical properties of plastic products.
Lastly, the content of other chemical components and metal impurities in calcium carbonate is also a factor that requires attention. The presence of these impurities may impact the quality and performance of calcium carbonate and its derivative products.
In summary, the quality technical indicators of calcium carbonate encompass multiple aspects, including calcium content, whiteness and color shade, moisture and volatile content, particle size distribution, particle shape, and other component content. Comprehensive consideration of these indicators is crucial for ensuring the quality of calcium carbonate and its derivative products.