October 26, 2024 – Ethylene and advanced α-olefin copolymers are attracting significant attention in the plastics industry due to their unique physical cross-linking properties and thermoplastic elastomer behavior. Among them, ethylene-octene copolymers stand out as a rapidly developing category and have become the preferred material in numerous applications. Dow’s Polyolefin Plastomers (POP) Affinity and Polyolefin Elastomers (POE) Engage, along with the recently emerged Olefin Block Copolymers (OBC), are leading the way in this field.
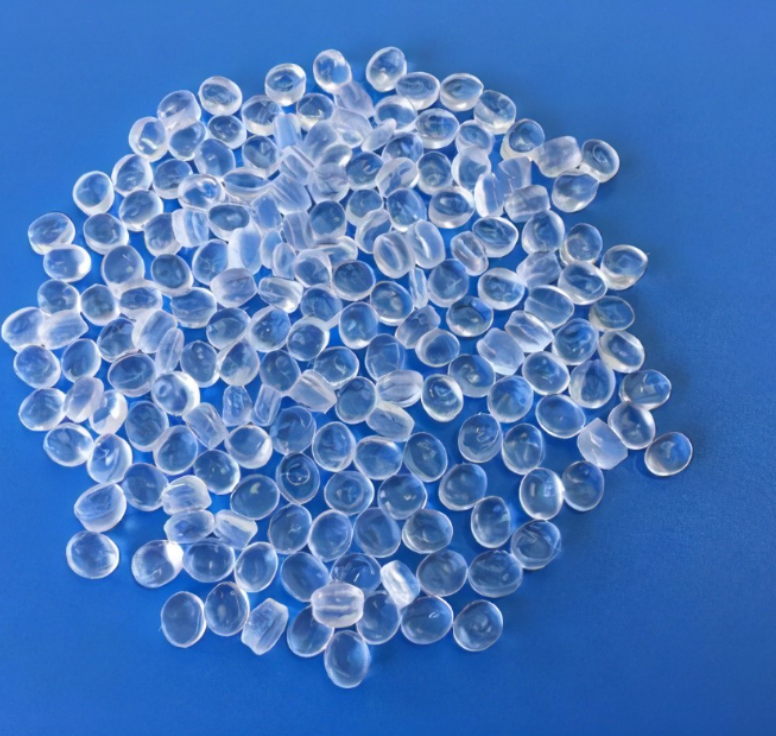
POP is renowned for its narrow molecular weight distribution, excellent physical properties, and processing performance. According to Color Masterbatch Industry News, Affinity, a metallocene polyolefin plastomer produced by Dow using INSITE technology, typically has an octene mass fraction below 20% and a density range of 0.875 to 0.935 g/cm3. Its superior heat-sealing performance, puncture resistance, impact strength, and transparency make Affinity widely used in food packaging, hygiene and medical products, elastic films, and personal care items. Additionally, POP is suitable for durable applications, such as hot-melt adhesive formulations, where it demonstrates strong bonding strength.
In contrast to POP, POE has a higher comonomer content (usually exceeding 20%), resulting in a relatively lower density. Engage, Dow’s metallocene polyolefin elastomer, not only exhibits excellent physical and mechanical properties and low-temperature performance but also shows remarkable heat aging and UV resistance due to its saturated molecular chain structure and narrow molecular weight distribution. POE has great potential in plastic toughening modifications and can be widely used in automotive parts, durable goods, extrusions, molded parts, and various other products. Furthermore, POE can replace traditional materials like rubber and flexible PVC, providing more environmentally friendly and efficient solutions across different sectors.
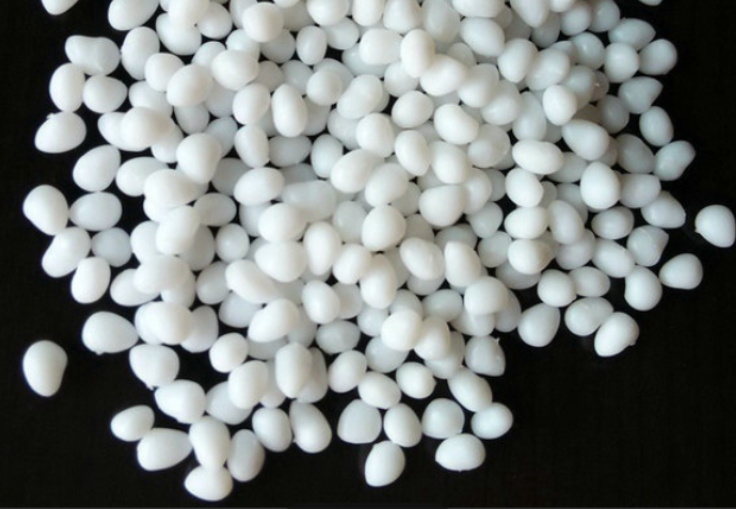
In recent years, with continuous technological advancements, Olefin Block Copolymers (OBC) have gradually emerged. As a new type of polyolefin thermoplastic elastomer, OBC significantly improves upon traditional POE in terms of performance. Especially in PP systems, OBC demonstrates outstanding low-temperature toughness and heat resistance. Its high melt index (MI) also provides excellent flowability, enhancing production efficiency. Although OBC’s application areas are not yet as extensive as POE’s, its applications are gradually expanding as its properties are further studied.
In terms of OBC’s application directions, PE-based and PP-based OBC cater to different occasions. For instance, in the packaging industry, PP-based OBC is favored for its good transparency and dispersibility, while in the footwear industry, PE-based OBC is highly regarded for its heat resistance, softness, abrasion resistance, and excellent compression set resistance at high temperatures. Moreover, OBC can serve as a bridge between PP and PE, combining the two closely to create a wide range of flexible formulations that meet specific needs in blends and multilayer structures.
In summary, ethylene and advanced α-olefin copolymers, along with their derivatives POP, POE, and OBC, play a pivotal role in the plastics industry. Their unique properties and application areas have injected new vitality into the development of the plastics industry. Looking ahead, with continuous technological progress and innovation, these materials are poised to showcase infinite possibilities in even more fields.