May 26, 2025 – Polycarbonate (PC): A Dual-Edged Sword of Transparency and Toughness in Modern Applications
Polycarbonate (PC), an engineering plastic celebrated for its blend of transparency and resilience, has carved a significant niche in both daily life and industrial sectors. From the luminous headlight casings of automobiles to the sleek exteriors of electronic devices, and from durable safety helmets to robust water dispenser barrels, PC’s “tough yet transparent” nature has made it a go-to material across diverse industries. However, like any material, PC is not without its challenges—chief among them are yellowing and cracking, which continue to perplex engineers worldwide.
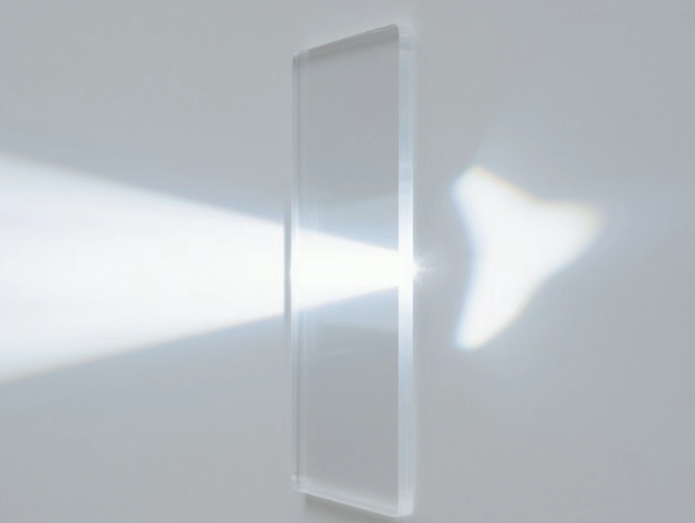
To unravel the mysteries behind PC’s yellowing and cracking, we must delve into its molecular architecture. PC, or polycarbonate in full, is typically synthesized through a condensation polymerization process using bisphenol A (BPA) and diphenyl carbonate as primary reactants. BPA imparts a rigid, high-strength backbone to PC, while the carbonate linkages act as flexible connectors, endowing the material with exceptional optical clarity, mechanical robustness, and thermal resistance. This unique molecular framework renders PC an ideal candidate for applications demanding both optical transparency and structural integrity.
Yet, this very molecular structure is the root cause of PC’s susceptibility to yellowing and cracking. PC’s transparency stems from its amorphous, non-crystalline nature—its molecular chains fail to align into ordered crystals upon cooling, resulting in a disordered, “glassy” state. While this non-crystalline structure grants PC its optical transparency, it also renders it vulnerable to molecular chain degradation, oxidation, or subtle structural alterations when exposed to heat, oxygen, or ultraviolet (UV) light, leading to yellowing over time.
According to industry insights from Color Masterbatch Industry Network, PC’s yellowing is primarily triggered by photo-oxidation and impurity-induced reactions. The carbonate bonds within PC’s backbone are prone to cleavage under the combined influence of UV radiation, heat, trace moisture, and metal ions, generating colored byproducts such as quinones. These substances absorb blue light and reflect yellow light, gradually causing the PC material to take on a yellowish hue.
PC’s propensity for cracking, on the other hand, stems from a combination of its amorphous structure, internal stresses, and environmental stressors. The weak intermolecular forces between PC’s molecular chains, due to its non-crystalline nature, result in ineffective stress dispersion, leading to localized stress accumulation. During injection molding, the rapid cooling and demolding of PC under high temperatures and pressures can induce internal stresses through phenomena such as molecular chain orientation freezing, residual temperature gradient stresses, and the formation of rigid surface layers upon contact with the mold. These internal stresses, when subjected to external forces or certain chemicals during use, can precipitate cracking.
Moreover, recycled polycarbonate (rPC) exhibits heightened susceptibility to yellowing and cracking. Having already endured UV exposure, thermal aging, and hydrolytic degradation during its initial service life, the “wounds” sustained by the raw material are exacerbated during the high-temperature extrusion and compounding processes of recycling, rendering rPC more prone to yellowing and cracking than virgin PC.
To mitigate these vulnerabilities in PC, improvements can be implemented at multiple levels—molecular design, injection molding, and end-use maintenance. At the molecular design stage, selecting raw materials or copolymer monomers with enhanced heat and oxidation resistance, controlling residual catalyst and oligomer content, and incorporating anti-yellowing additives can boost anti-aging performance. During injection molding, optimizing melt temperature, mold temperature, cooling rates, and demolding techniques can minimize stress concentration. In end-use applications, avoiding prolonged UV exposure, contact with solvents like alcohol and gasoline, and rough handling or impact can prolong the service life of PC products.
In conclusion, PC is not an inherently problematic material; rather, its effective utilization hinges on scientific and rational application and maintenance. By doing so, we can fully harness the advantages of PC, unlocking a world of convenience and possibilities for our lives and industries.