March 18, 2025 – The pigment dispersion process stands as a pivotal step in the production of color masterbatch, its significance undeniable as it directly impacts the storage stability, application effectiveness, aesthetic appearance, and various performance indicators of the masterbatch. Consequently, the judicious selection of dispersants emerges as a critical aspect of the production process.
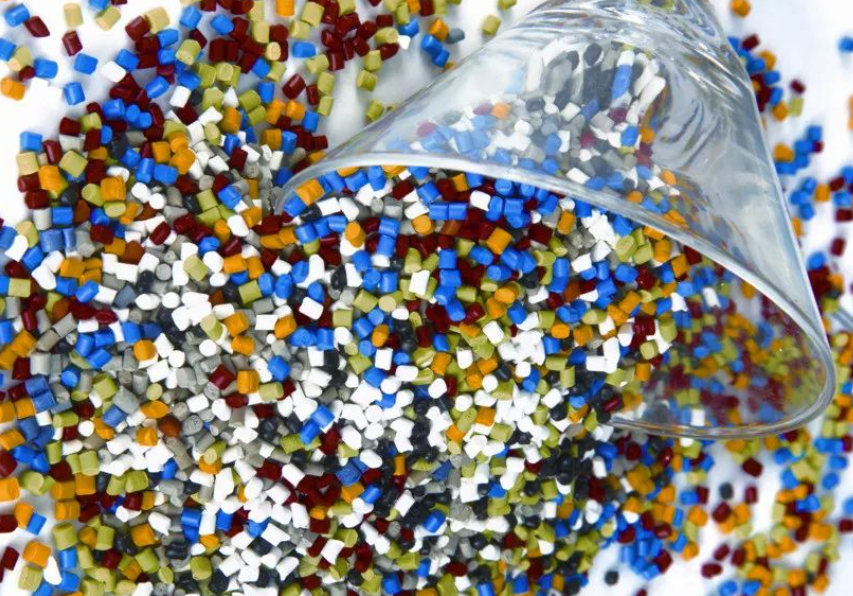
As the name suggests, dispersants primarily function to evenly distribute various powdery substances within a solvent. By leveraging specific charge repulsion principles or high-molecular-weight steric effects, dispersants ensure the stable suspension of solid particles in a solvent (or dispersion liquid). These substances possess both hydrophilic and lipophilic properties within their molecular structure, allowing them to uniformly disperse solid particles of inorganic and organic pigments that are otherwise difficult to dissolve in liquids. Additionally, they effectively prevent the sedimentation and agglomeration of solid particles, serving as indispensable agents for forming stable suspensions. According to insights from the Color Masterbatch Industry Network, the application of dispersants in color masterbatch production plays a vital role in enhancing product quality and performance.
Among the various types of dispersants, fatty acids, aliphatic amides, and esters hold significant positions. For instance, when stearamide is used in conjunction with higher alcohols, it notably improves lubricity and thermal stability, with typical usage levels ranging from 0.3% to 0.8%. It also serves as a slip agent for polyolefins. Octadecenyl bis-stearamide, also known as ethylene bis-stearamide, is a high-melting-point lubricant used in quantities between 0.5% and 2%. Other examples include glyceryl monostearate, glyceryl tristearate, and oleoyl, which are generally used in amounts of 0.2% to 0.5%. Hydrocarbon paraffin solids, with melting points ranging from 57 to 70°C, are insoluble in water but soluble in organic solvents. However, their dispersion, compatibility, and thermal stability in resins are relatively poor, limiting their usage to typically below 0.5%.
Paraffin-based dispersants are also noteworthy. Although paraffin itself acts as an external lubricant, its non-polar straight-chain hydrocarbon nature prevents it from wetting metal surfaces, thus failing to prevent the adhesion of resins like PVC to metal walls. Optimal synergistic effects are achieved only when used in combination with substances such as stearic acid or calcium stearate. Liquid paraffin, with a freezing point range of -15 to -35°C, exhibits relatively poor compatibility with resins during extrusion and injection molding processes. Consequently, its addition is generally controlled between 0.3% and 0.5%, as excessive amounts can degrade processing performance. Microcrystalline wax, derived from petroleum refining, has a relatively high molecular weight and numerous isomers, with a melting point range of 65 to 90°C. It offers good lubricity and thermal stability but relatively poor dispersion, typically used in amounts of 0.1% to 0.2%, preferably in conjunction with substances like butyl stearate or higher fatty acids.
Metallic soap dispersants represent another major category, referring to metal salts of higher fatty acids. For example, barium stearate is suitable for various plastics, with a typical usage of around 0.5%. Zinc stearate is appropriate for plastics like polyolefins and ABS, used at 0.3%. Calcium stearate is more suited for external lubrication in general-purpose plastics, with a usage range of 0.2% to 1.5%. Other metallic soap dispersants include cadmium stearate, magnesium stearate, and copper stearate.
Low-molecular-weight wax dispersants also possess unique application value. These dispersants are a series of low-molecular-weight polymers produced from various polyethylenes (homopolymers or copolymers), polypropylenes, polystyrenes, or other polymer modifications through processes like cracking and oxidation. The main products include homopolymers, oxidized homopolymers, ethylene-acrylic acid copolymers, ethylene-vinyl acetate copolymers, and low-molecular-weight ionomers. Among them, polyethylene wax (chemically known as polyethylene glycol, PEG (Poly Ethylene Glycol)) is widely used due to its exceptional performance.
Dispersants play multiple roles in color masterbatch production, including enhancing gloss, preventing color floating and mottling, improving color strength, reducing viscosity to increase pigment loading, increasing storage stability, enhancing color development and saturation, and increasing transparency (for organic pigments) or opacity (for inorganic pigments). When selecting dispersants, factors such as dispersion performance, compatibility with resins and fillers, thermal stability, flowability during processing, and impact on product performance must be comprehensively considered. Additionally, the amount of dispersant used must be strictly controlled, typically at around 5% of the masterbatch mass.