November 18, 2024 – Polypropylene (PP), a pivotal thermoplastic resin in the chemical industry, hinges on meticulous selection of its production materials. The manufacturing process of polypropylene encompasses as the core ingredient, alongside catalysts and an array of auxiliary materials, forming the bedrock of its production.
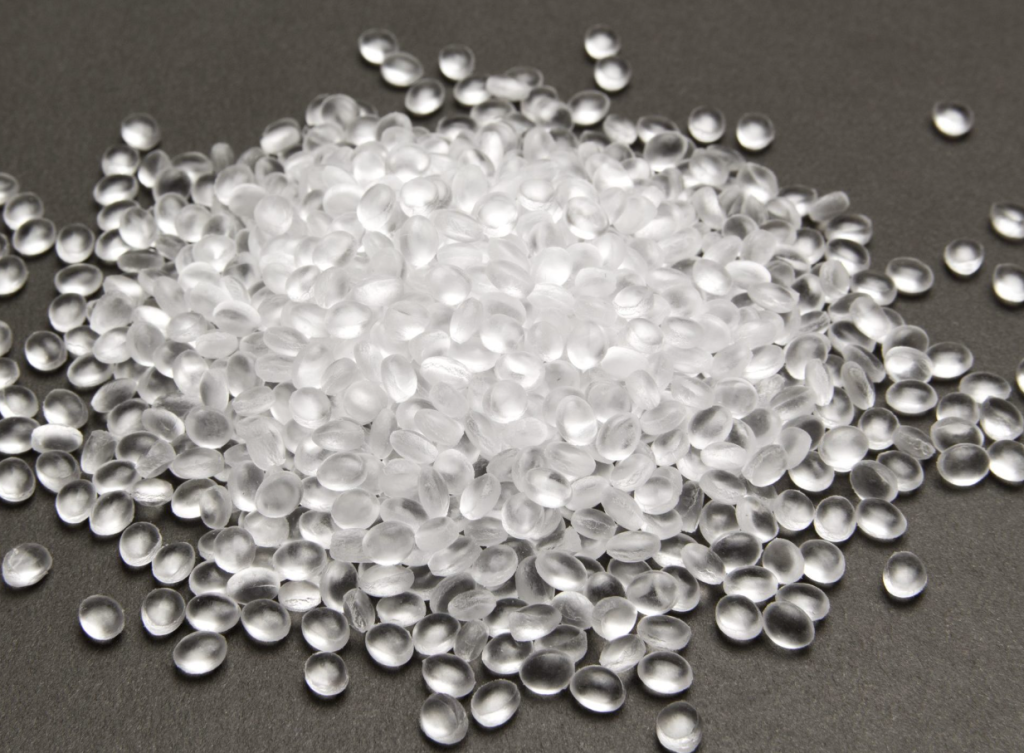
The core raw material, propylene monomer, is primarily refined through intricate processes such as catalytic cracking and steam cracking in petroleum refining. These processes are vital links in the petrochemical chain, where various distillates are separated from crude oil to obtain propylene.
Catalysts play an indispensable role in polypropylene production. For instance, Ziegler-Natta catalysts, with their high catalytic efficiency and selectivity, precisely regulate the molecular structure of polypropylene, imparting specific performance advantages to the product. Metallocene catalysts, on the other hand, excel in producing polypropylene with special properties like high transparency and rigidity, thereby broadening the scope of polypropylene applications.
Beyond these core materials, a suite of auxiliary materials is also essential in the production process. Hydrogen, for example, is used to finely adjust the molecular weight distribution of polypropylene, optimizing its processing characteristics. The addition of antioxidants effectively prevents oxidative degradation of the polymer during processing and subsequent usage, ensuring long-lasting stability of the product.
According to AsiaMB, the selection of raw materials for polypropylene production is not arbitrary but a multifaceted consideration. Cost stands as the primary concern, with fluctuations in the market price of propylene monomer directly impacting the production costs of polypropylene. Manufacturers must closely monitor petroleum market dynamics to secure the most cost-effective propylene supply solutions.
Product performance requirements are equally critical. Various application fields impose distinct performance demands on polypropylene, ranging from high strength and heat resistance for automotive component manufacturing to transparency and hygienic safety for food packaging. This underscores the significance of material selection tailored to specific applications.
Furthermore, the adaptability of production processes imposes stringent requirements on raw material choice. Different processes have clear indicators for material purity and impurity content. Companies must carefully select materials that meet these standards, based on their own process conditions, to ensure stable and efficient production workflows.
In summary, the selection of raw materials for polypropylene production is a complex process involving multiple dimensions such as cost, performance requirements, and production processes. Only through scientific and reasonable material choices can polypropylene products that meet market demands while maintaining high quality be produced.