May 9, 2025 – With the automotive industry booming, plastic components have become increasingly indispensable in vehicle manufacturing and maintenance. The quality of bonding techniques applied to these plastics is a make-or-break factor for a car’s overall performance and safety, sparking intense interest in identifying the most suitable bonding approach.
Three primary methods dominate the bonding of automotive plastic parts: solvent bonding, adhesive bonding, and hot melt bonding. Solvent bonding operates by using solvents to dissolve the surface of plastics. Once the solvent evaporates, the two parts merge seamlessly. This method is particularly effective for thermoplastics like polyvinyl chloride (PVC) and polystyrene, praised for its simplicity, low cost, and robust bonding results.
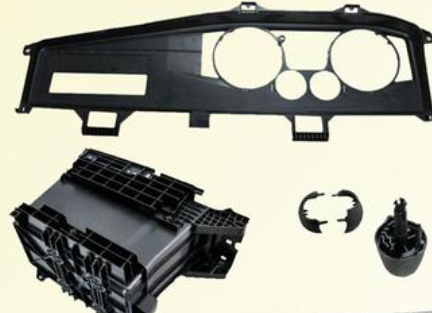
Adhesive bonding leverages diverse adhesives, such as epoxy and polyurethane, to bond various materials, including thermosetting plastics. Its strengths lie in high bonding strength and excellent chemical resistance. However, it comes with notable drawbacks, such as higher costs and longer curing times. Hot melt bonding involves heating the plastic surfaces until they melt and then pressing them together. Ideal for thermoplastics like polypropylene and polyethylene, it offers rapid bonding and reliable strength but demands specialized equipment and has a steep learning curve.
According to AsiaMB, choosing the right bonding method in practice requires a comprehensive assessment of multiple factors. The nature of the plastic material is paramount, as thermoplastics and thermosetting plastics require different bonding strategies. Bonding strength requirements also play a crucial role; when high durability is needed, adhesive bonding is often the preferred choice. The operating environment matters too. For on-site operations, solvent and adhesive bonding provide greater flexibility, while hot melt bonding can significantly boost efficiency when professional equipment and facilities are available.
It’s crucial to recognize the potential risks associated with these bonding techniques. Solvent bonding releases harmful gases that endanger operators’ health and may create bubbles during evaporation, weakening the bond. The lengthy curing process of adhesive bonding can slow down production, and some adhesives are sensitive to temperature and humidity, affecting performance stability. Hot melt bonding’s reliance on specialized equipment drives up costs, and improper temperature control can cause plastic deformation, ruining the bonding effect. Only by fully understanding the features and limitations of each method can the automotive industry secure the best bonding solutions for plastic components.