May 27, 2025 – Syensqo, a global leader in specialty materials, has recently announced the successful completion of a major expansion of its compounding production lines at its Changshu plant in China. The expanded lines, now fully operational, cover compounding capabilities for high – end products such as Amodel® PPA, Ryton® PPS, Kalix® HPPA, Omnix® HPPA, and Ixef® PARA. This move is aimed at meeting the surging demand for specialty materials in industries like electric vehicles, semiconductors, smart devices, and healthcare.
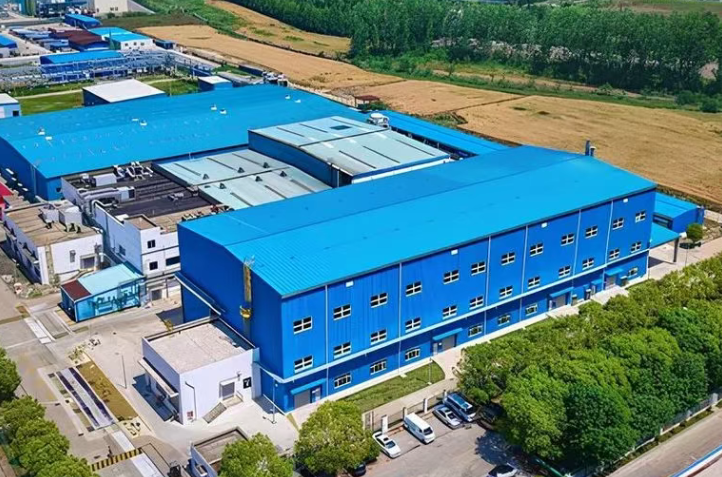
According to the Color Masterbatch Industry Network, in the automotive and electronics sectors, the application penetration rate of specialty nylon, a high – performance polyamide (PA) material, is on the rise. Although PA6/PA66 still dominate the market, their specialty nature has weakened with the gradual release of production capacity. In contrast, materials with specific performance requirements, such as high – temperature nylon, are being increasingly used in key automotive components like fuel lines, fuel caps, and brake lines. These are precisely the focus of Syensqo’s recent expansion.
PPA (polyphthalamide), a partially aromatic PA made from isophthalic acid or terephthalic acid, offers an excellent balance between cost and performance, filling the market gap between traditional engineering plastics and high – cost specialty polymers. Since Amoco (later produced by Solvay) launched the Amodel® PPA product line in 1991, PPA has been widely used globally. Products like DuPont/Celanese’s Zytel®, Mitsui’s Arlen® series in Japan, and PA6T, PA9T all fall within the PPA category defined by ASTM.
PPA shows remarkable advantages in heat resistance. Its heat distortion temperature can reach over 300℃, continuous use temperature is up to 170℃, and the glass transition temperature is around 130℃. Compared with PA66, PPA significantly improves the heat – resistant temperature by introducing a large number of benzene rings into the main chain of macromolecules, although it needs to be copolymerized with other aliphatic diacids or diamines to improve processability. HPPA, a high – performance polyamide material, includes PPA and Ixef® PARA, featuring excellent high – temperature resistance, mechanical strength, chemical resistance, and dimensional stability. Syensqo’s Kalix® HPPA, a high – glass – fiber – filled composite material, is designed for structural components in smart mobile electronics and medical devices, and can replace metal materials. In addition, Syensqo is also actively responding to the market demand for sustainable materials by launching a series of bio – based products, such as Kalix® 2000 base resin with 61% bio – based content.
Notably, on May 14, Syensqo also announced an expansion plan for PPS (polyphenylene sulfide). The company will invest to enhance the compounding production capacity of its Ryton® PPS at the Augusta production site in Georgia, USA. This plant mainly serves the automotive industry and has the capacity to mass – produce specialty engineering plastics like PPA and PEEK. PPS has a wide range of downstream applications. Besides the automotive industry, it also covers fields such as electronics and electrical engineering, the machinery industry, petrochemicals, the pharmaceutical industry, light industry, and special fields like military and aerospace. With the continuous emergence of high – performance specialty fibers and films, PPS is finding more and more applications in the environmental protection and clean energy sectors. Currently, the global PPS production capacity is centered in Asia, especially in Japan. As one of the world’s largest PPS producers, Japan has several important manufacturers including DIC. China, another significant production base, started late but has been developing rapidly. By 2019, its total production capacity had reached about 46,500 tons, showing a steady growth trend.