May 19, 2025 – In electronics chip fabrication facilities, sterile operating rooms, and other static-sensitive environments, the protective gear worn by staff and various plastic products predominantly feature a black appearance. As AsiaMB has learned, over 85% of anti-static plastic products on the market today are black—a phenomenon rooted in the deep technical logic of materials science and industrial application.
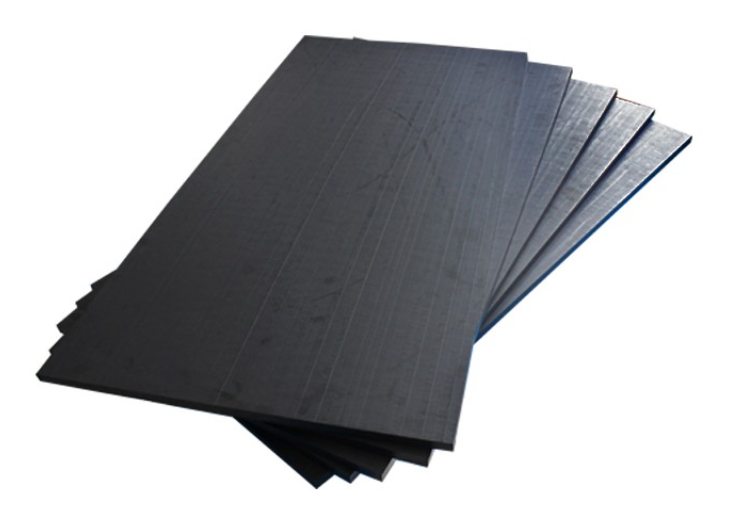
Static electricity, a physical phenomenon caused by charge imbalance on object surfaces, manifests as harmless sparks from clothing friction in daily life but poses severe safety hazards in industrial settings. For example, a mere 100V static voltage can damage delicate chips in electronics manufacturing, while static interference in medical environments may corrupt data from monitoring devices. Consequently, the performance of anti-static materials has become a critical factor in ensuring production safety and equipment stability across semiconductor, medical, and other high-precision industries.
The technological breakthrough behind anti-static plastics lies in the composite design of conductive fillers and resin matrices. These materials use resin as a base and incorporate 3%-5% conductive carbon black to form internal conductive networks, enabling rapid static dissipation. As nanoscale carbon particles, conductive carbon black’s unique chain-like structure reduces the surface resistance of plastic products to 10⁶-10¹¹Ω, meeting industrial anti-static standards. However, this high-performance filler’s strong light-absorbing property dictates that products must appear black when the filler reaches effective concentrations—explaining the dominance of black anti-static products in the market.
Despite the color limitation, black anti-static plastics have solidified their market position due to significant comprehensive advantages. Data shows they are priced 20%-30% lower than light-colored counterparts while offering stable conductivity and mature processing techniques. Notably, advancements in nanodispersion technology have enabled some companies to develop transitional colors like dark gray and dark green, providing more options for specialized scenarios. Looking ahead, the research and application of new conductive materials—such as metal oxides and carbon nanotubes—may drive anti-static plastics toward high-performance, multi-color solutions.
Under current technical constraints, black anti-static plastic products remain the “workhorse” for combating static hazards in industrial settings. From chip production lines to sterile operating rooms, their understated appearance quietly safeguards precision manufacturing and medical safety, exemplifying the balance between material performance and industrial needs.