December 15, 2024 – Addressing the Persistent Challenge of Bubble Rupture in PVC Skin Foam Board Production
In the production of PVC skin foam boards, bubble rupture remains a significant hurdle for manufacturers. This article delves into the typical causes of bubble rupture in PVC skin foam boards and proposes corresponding countermeasures to help producers tackle this issue more effectively.
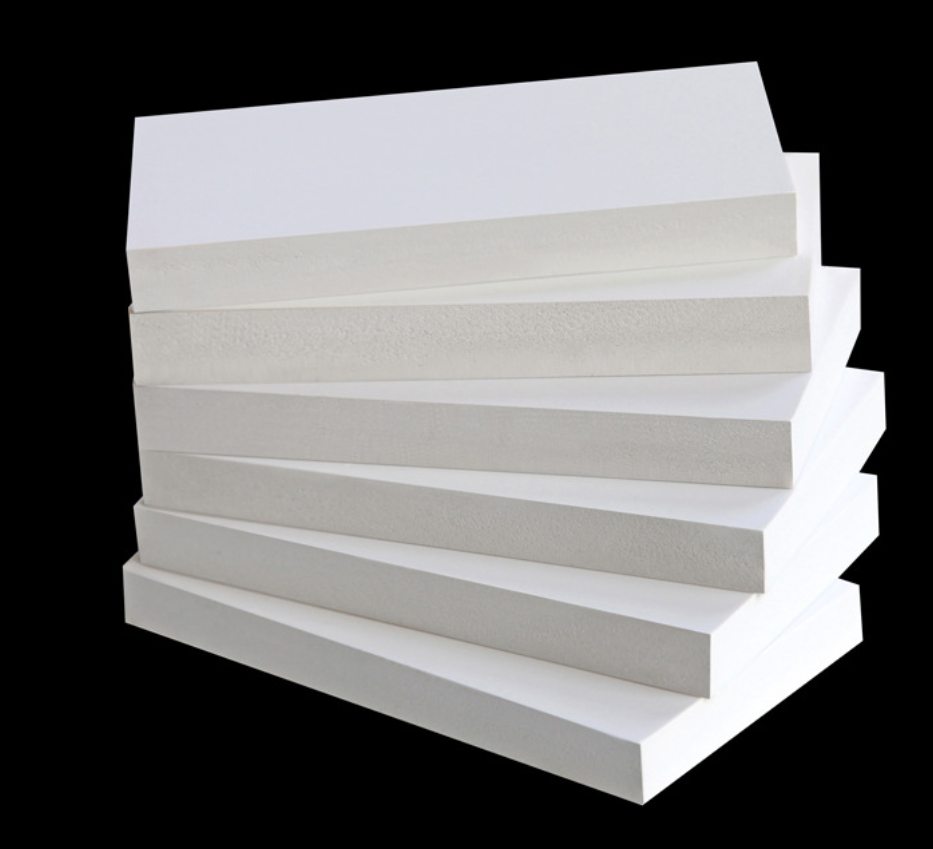
The selection of PVC resin plays a pivotal role in the foaming process. According to AsiaMB, different types of PVC resins exert notable influences on the foaming effect. Resins with low molecular weight or degree of polymerization can lead to inadequate melt strength, making bubble rupture more likely. Therefore, producers should carefully choose PVC resins and strictly control their viscosity to ensure the quality of the final board.
Melt thermal stability is another critical factor. Poor plasticization of the melt or improper control of extrusion temperatures can both result in decreased melt strength and subsequent bubble rupture. To mitigate this, producers should regularly test the performance of stabilizers and adjust dosages accordingly. Simultaneously, maintaining strict control over extrusion temperatures is essential to prevent melt degradation during the extrusion process.
The addition of foaming agents also significantly impacts the foaming effect. Incorrect usage, such as excessive amounts or inappropriate types, can cause rapid internal pressure increases within bubbles, leading to oversized pore sizes and disrupted pore structures. Thus, producers must carefully select and blend foaming agents, controlling their usage based on product requirements.
Furthermore, the quality of processing additives cannot be overlooked. Poor-quality additives or insufficient dosages can weaken the foam’s structure, resulting in bubble rupture. To address this, producers should opt for high-quality processing additives and adjust dosages based on factors such as board thickness.
The dosage, particle size, and activity of calcium carbonate also play crucial roles in the foaming process. Excessive amounts, large particles, or low activity can all contribute to reduced melt strength and increase the likelihood of bubble rupture during bubble expansion. Therefore, producers should closely monitor these parameters and, if necessary, increase the use of foaming regulators.
The choice of mold also significantly affects the foaming effect. Different thicknesses of skin foam plastic boards require different die designs. Improper mold usage, such as using a thick board die for thin board production, can increase flow resistance and cause uneven material extrusion, leading to bubble rupture. Hence, producers should select the appropriate die before production to ensure compatibility with the board’s thickness.
Lastly, uneven foaming or material extrusion across the board’s cross-section is a common cause of bubble rupture. To address this, producers should strictly adhere to formulas and process operating procedures, carefully analyze instances of bubble rupture, and employ different solutions based on the underlying causes. Adjustments to die bolts, temperatures, or the gap between shaping templates may be necessary.
In summary, the issue of bubble rupture in PVC skin foam board production encompasses multiple aspects. Producers should comprehensively analyze and address this problem by focusing on resin selection, melt thermal stability, foaming agent addition, processing additive quality, calcium carbonate usage, mold selection, and the uniformity of board cross-section foaming or material extrusion. By doing so, they can enhance product quality and production efficiency.