May 23, 2025 – In the plastics industry, the optical appeal of products—particularly their luster and texture—plays a pivotal role in defining both aesthetic value and functionality. Pearlescent masterbatch and matte masterbatch, two distinct optical modification materials, offer contrasting visual and tactile experiences: one mimicking the iridescent shimmer of natural pearls, the other creating a subtle, frosted finish. Their applications span diverse sectors, from luxury cosmetic packaging to anti-glare electronics, shaping the visual landscape of everyday products.
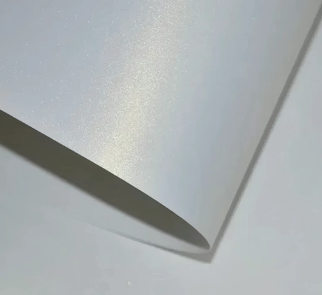
一、Pearlescent Masterbatch: Industrial Reproduction of Natural Iridescence
Optical Principles and Material Composition
The captivating iridescent effect of pearlescent masterbatch stems from its core component: layered pearlescent pigments such as mica titanium and bismuth oxide. These pigments create a pearl-like sheen through light interference, refraction, and reflection on their lamellar structures. Take mica titanium as an example: its color varies with the thickness of the titanium dioxide (TiO₂) coating on the mica substrate. A 60–80 nm TiO₂ layer produces silver-white hues, 100–120 nm yields gold, and 140–160 nm results in red. Innovations in material science have seen synthetic mica replace natural mica, with heat resistance exceeding 300°C to accommodate high-temperature injection molding processes.
Manufacturing Processes and Challenges
Dispersion technology is critical in producing pearlescent masterbatch. Due to the agglomeration tendency of pearlescent pigments, surface modification with silane coupling agents and high-precision blending via twin-screw extruders are essential to preserve pigment lamellae. Carrier resin compatibility is equally vital; matrix resins must match the pigment’s polarity, often using maleic anhydride-grafted polypropylene to enhance adhesion.
Performance Advantages and Limitations
Pearlescent masterbatch offers high gloss, vivid color saturation, and excellent weather resistance. However, it faces challenges such as higher costs, restricted processing temperatures, and opacity that limits use in transparent applications.
二、Matte Masterbatch: The Functional Revolution of Understated Texture
Matte Mechanisms and Material Innovations
Matte effects rely on light diffusing through micro-roughness on the plastic surface. Extenders like fumed silica (inorganic) create porous surfaces, while talcum powder reduces gloss via physical filling. Organic extenders such as polyethylene wax and erucamide offer both matting and lubricating properties. According to the Color Masterbatch Industry Network, different extenders impact secondary properties like mechanical strength to varying degrees.
Process Optimization
Nano-dispersion technology is key in matte masterbatch production. Ultrasonic pretreatment of extenders, combined with multi-zone temperature control in twin-screw extruders, ensures uniform dispersion. Mechanical balance is critical: adding over 5% extender can reduce tensile strength by 20%, necessitating toughening agents like elastomers for compensation.
Performance Characteristics and Applications
Matte masterbatch provides low gloss, fingerprint resistance, and cost efficiency but struggles with low light transmittance and risks of organic extender migration at high temperatures.
Pearlescent and matte masterbatch represent two primary technical directions in plastic optical modification, rooted in film interference and surface scattering principles, respectively. Their collaborative innovation drives aesthetic upgrades in plastic products while serving as core materials for automotive lightweighting, functional electronics, and sustainable packaging. Moving forward, precise mechanistic research, continuous process optimization, and cross-disciplinary innovation will be pivotal to advancing this dynamic industry.