September 14, 2024 – The color masterbatch industry, a cornerstone in the realm of plastic coloring, continues to thrive on the strength of its superior pigmentation, eco-friendliness, and ease of storage and transportation. This high-polymer composite coloring material is meticulously crafted through a multi-step process, beginning with a color resin base that is infused with a plethora of dispersants, pigments, and functional additives. The material is then refined through melt blending, extrusion, high-speed mixing, and cooling pelletization.
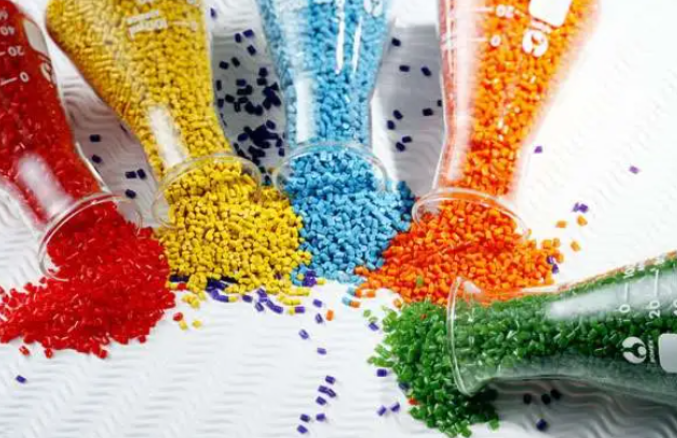
Pigment selection plays a pivotal role in the composition of color masterbatches. Titanium dioxide is the preferred choice for white masterbatches, while carbon black lends its deep, rich hue to black masterbatches. Colorful masterbatches, on the other hand, boast a diverse array of pigments, including azo, phthalocyanine, and metal oxides. Polyethylene resin, the core component of color masterbatches, undergoes precise melt cutting and fine processing to ensure that pigments are uniformly and securely adhered to the resin, guaranteeing lasting and stable coloration.
To enhance the processing fluidity of color masterbatches and improve pigment dispersion within the resin, the use of dispersants has become crucial. Commonly used dispersants, such as amide waxes and polyolefin waxes, effectively promote uniform pigment dispersion, thereby boosting the overall performance of color masterbatches. Furthermore, functional color masterbatches have emerged to cater to the specific needs of plastics manufacturers. These masterbatches not only color plastics but also impart special properties such as UV resistance, weather resistance, and antistatic capabilities, thereby accommodating a wider range of applications.
Among the various types of color masterbatches, universal masterbatches are particularly favored for their broad applicability. Their carriers can be composed of low-molecular-weight polyethylene wax, EVA, and other materials, and can be compounded as needed. To increase pigment content and reduce the amount of masterbatch required, universal masterbatches are formulated with a high proportion of pigments, ensuring rich and long-lasting coloration. Meanwhile, the market offers a diverse range of formulations for black, white, and color masterbatches to meet different demands.
Additionally, specialized products such as filler masterbatches and cooling masterbatches have injected new vitality into the color masterbatch industry. Filler masterbatches, primarily composed of inorganic materials like calcium carbonate, effectively reduce the cost of plastic products while enhancing their performance. Cooling masterbatches, on the other hand, incorporate peroxide and other additives to lower the temperature during polypropylene spinning, thereby improving the spinning process and expanding the application scope of polypropylene.
In conclusion, the color masterbatch industry, through continuous innovation and development, is providing the plastics industry with more diverse, efficient, and environmentally friendly coloring solutions. As technology advances and the market expands, the color masterbatch industry is poised to embrace even broader development prospects and a brighter future.