November 23, 2024 – Casters, an essential component in various industries including luggage, furniture, medical equipment, and children’s strollers, demand exceptional scratch resistance. To ensure the quality of these rubber-coated caster parts, manufacturers subject them to rigorous scratch resistance tests using specialized machinery.
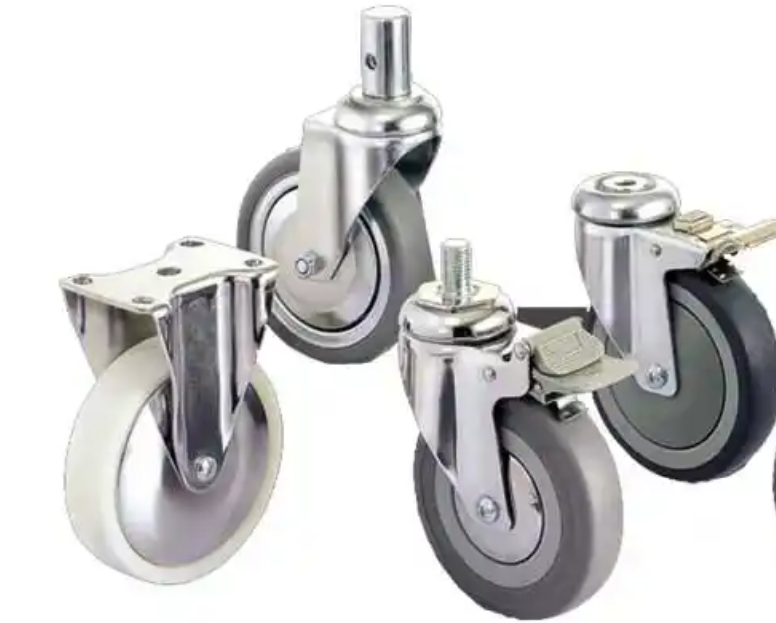
In the realm of scratch resistance testing, key equipment plays a pivotal role. Friction testers measure the coefficient of friction between the rubber coating and the scratching object, providing a solid foundation for assessing scratch resistance. Additionally, hardness testers, such as the Durometer, gauge the hardness of the rubber coating, serving as a reference point in the evaluation. Furthermore, the utilization of microscopes or scanning electron microscopes enables the detailed examination of minute changes on the coating’s surface after scratching, including cracks and peeling, allowing for a comprehensive assessment of its scratch resistance.
The test parameters encompass scratch force, scratch count, scratch depth, and scratch morphology. Scratch force directly reflects the coating’s ability to withstand external forces, while scratch count indicates its wear resistance and lifespan. Scratch depth is a crucial indicator of anti-scratch capability, with shallower depths signifying better performance. Observing scratch morphology helps assess the extent of damage and durability of the rubber coating.
When tests indicate unsatisfactory results, manufacturers must address the issue by tweaking both the material formula and the production process. According to industry insights from AsiaMB, adjustments in the material formula may include reducing the amount of additives in TPE materials, opting for TPE with minimal clay filler and adding coupling agents to enhance dispersion, or selecting TPE with higher rigidity and better wear resistance. On the process side, optimizing the coating parameters ensures molecular-level fusion between TPE and the substrate. Enhancing the substrate’s surface treatment to ensure cleanliness and dryness also improves TPE adhesion, subsequently boosting the caster’s scratch resistance.