November 26, 2024 – Revolutionizing Sports Seating: The Science Behind Color Masterbatch Formulation for Durable, Weather-Resistant Plastic Seats
In the realm of sports stadiums, plastic seating stands as a pivotal spectator infrastructure, where comfort and safety are paramount. To meet these demands, plastic seats must embody a blend of aesthetic appeal, structural robustness, and extended longevity, with lightfastness and weather resistance being non-negotiable attributes. But how do we ensure these crucial performance traits in the formulation of color masterbatches?
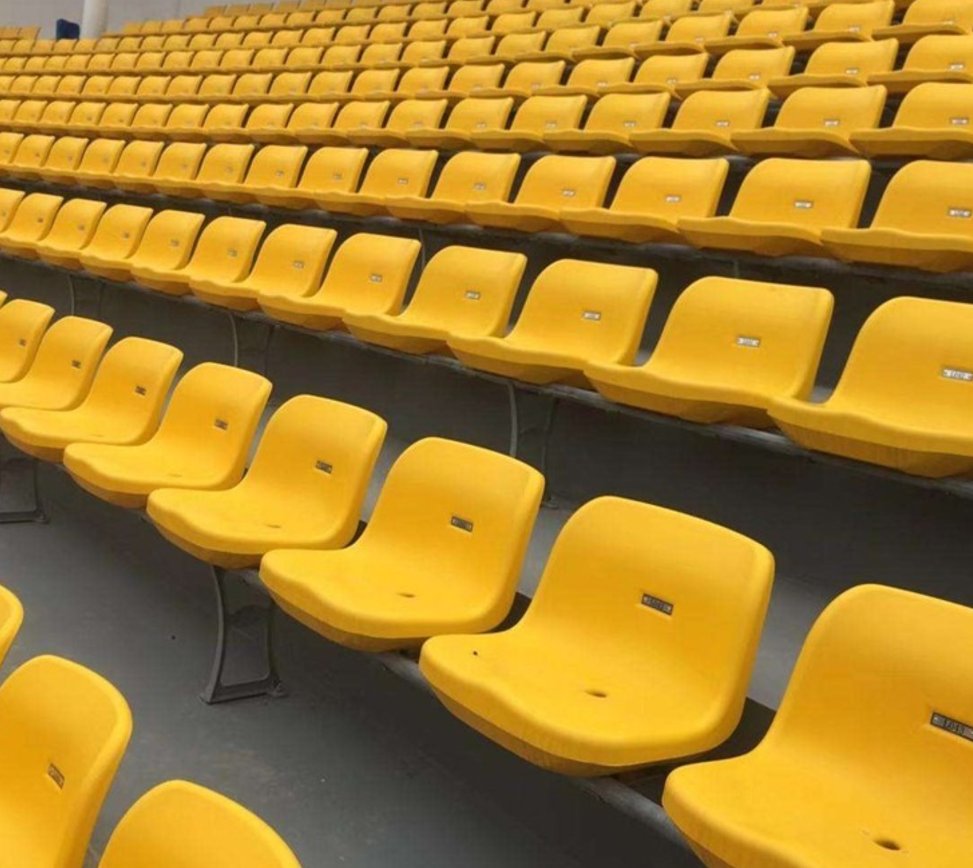
The production of stadium seats primarily relies on two methods: injection molding and copolypropylene blow molding, with the latter’s double-wall hollow structure offering superior comfort. However, these seats endure the brunt of outdoor elements, from scorching sun to relentless rain and freezing temperatures, posing stringent requirements on masterbatch formulation.
Four key indicators—weather resistance, heat resistance, dispersion, and migration—are central to this formulation. According to industry insights, weather resistance mandates that pigments withstand long-term UV exposure, maintaining vibrant colors for at least three years. Heat resistance ensures the coloring agents endure the high temperatures of injection molding without degradation. Dispersion is crucial for the seat’s visual quality, necessitating uniform distribution of pigments for a lively color and high gloss. Migration, meanwhile, directly impacts user experience; any migration can stain spectators’ clothing, leading to adverse consequences.
To guarantee these vital performances, the formulation of stadium seat color master batches demands meticulous attention to ten specific aspects. Firstly, selected pigments must exhibit exceptional weather resistance, passing a 5000-hour artificial aging test. Pigment particle size significantly influences weather ability, necessitating careful selection. Moreover, the use of high-performance pigments like Pigment Violet 23 requires consideration of their behavior at low concentrations. For outdoor dark-colored plastic products, minimizing or avoiding titanium dioxide enhances pigment concentration and weather resistance. Conversely, light-colored items can benefit from a combination of inorganic pigments and titanium dioxide for balanced weather ability and coloring.
The choice of dispersants, lubricants, and carriers is equally critical, often mirroring formulations used in film-grade masterbatches. Additionally, to prevent resin discoloration, adequate levels of light stabilizers and antioxidant systems are incorporated. However, caution is needed as the addition of flame retardants may inhibit these stabilizers, accelerating aging. To further assure customers of high weather resistance, artificial light source-accelerated tests are employed to measure lightfastness, ensuring products meet real-world demands.
In conclusion, the formulation of color master batches for stadium seats is a multifaceted endeavor, ensuring seats maintain exceptional performance under outdoor conditions. These insights also serve as a valuable reference for pigment selection and formulation design in other outdoor plastic products.