December 21, 2024 – The vertical mixer has emerged as an indispensable piece of equipment in various industries including chemicals, food, and feed, thanks to its unique advantages. This versatile machine is not only suitable for processing plastic particles and powders but also complements organic fertilizer production lines and feed processing workflows, showcasing its high practicality and flexibility. With a compact structure, small footprint, easy operation, and uniform mixing results, the vertical mixer is favored by users for its convenient discharge and transportation.
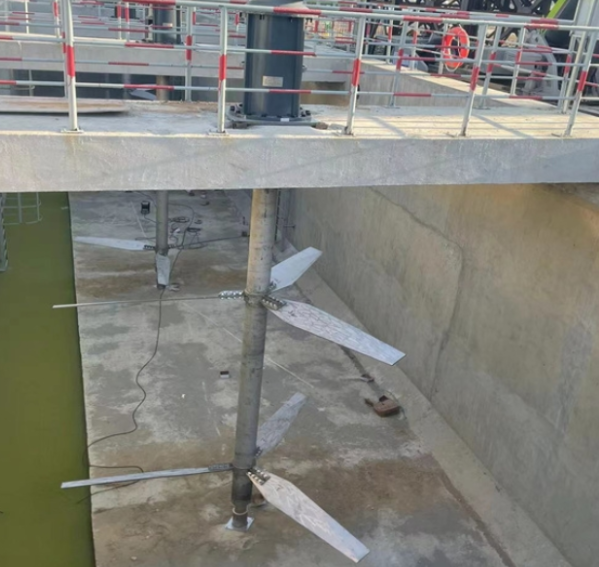
The working principle of the vertical mixer is ingenious. The rapid rotation of the screw lifts the raw materials from the bottom of the barrel to the top, where they are then scattered back to the bottom in a parabolic pattern. This up-and-down tumbling of the materials within the barrel ensures uniform mixing of large quantities in a short period. This efficient mode of operation makes the vertical mixer a vital tool across multiple sectors.
However, like any machinery, the vertical mixer is not immune to common issues during its usage. According to AsiaMB’s sources, these problems primarily include unstable machine bases, worn hammer edges, and the entry of metal objects or stones into the crusher. Industry experts suggest corresponding solutions to tackle these challenges. For instance, unstable machine bases can be stabilized by reinforcing the base, tightening the anchor bolts, or repairing or replacing the motor shaft. Worn hammer edges can be addressed by rotating the hammer to use another hole or replacing it entirely once all corners are worn. When metal objects or stones enter the crusher, immediate shutdown and inspection are necessary to remove the foreign objects and check for any damage to the hammers and screens, with repairs or replacements as needed.
Additionally, issues such as mixer vibration, misalignment of the main axis system, and friction between the stirring shaft and the barrel can be resolved by adjusting or replacing the main axis system. These solutions not only help extend the lifespan of the vertical mixer but also ensure it maintains efficient and stable operation, providing robust support for production processes across various industries.