September 27, 2024 – PPS and PPA: Two High-Performance Engineering Plastics Paving the Way for Automotive Innovation
In the realm of new energy vehicles, PPS (polyphenylene sulfide) and PPA (polyphthalamide) have emerged as two high-performance engineering plastics that are revolutionizing the automotive industry with their unique advantages. These materials are playing a crucial role in enabling lightweight designs and enhancing vehicle performance.
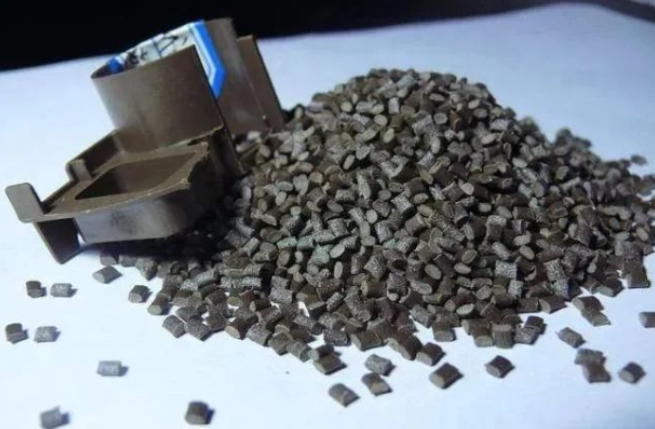
PPS, with its exceptional high-temperature resistance, chemical corrosion resistance, and mechanical strength, holds a prominent position in the new energy vehicle sector. According to industry sources, PPS maintains stable physical properties at temperatures exceeding 200°C, making it an ideal choice for engine compartment components and battery systems. Its outstanding mechanical performance and chemical corrosion resistance ensure the stability and reliability of automotive parts during long-term use. Furthermore, PPS’s excellent dimensional stability and flame retardancy further enhance its value in automotive manufacturing.
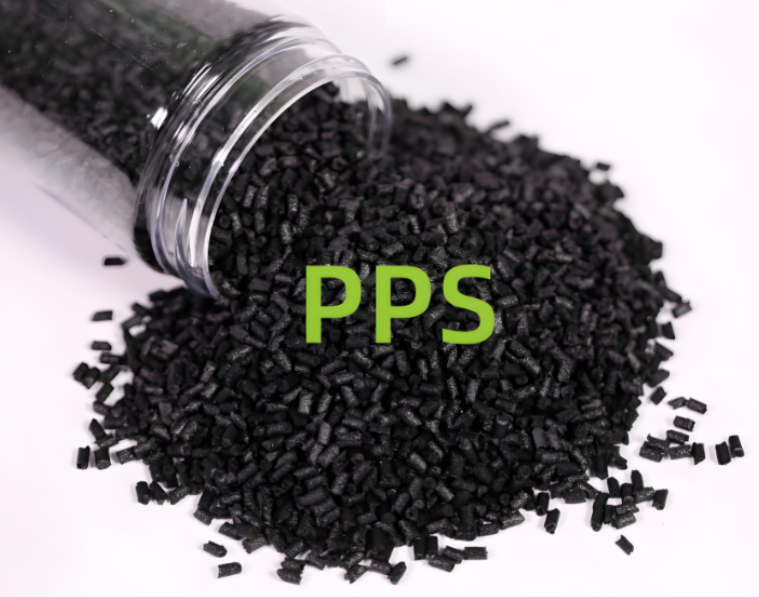
On the other hand, PPA stands out with its high heat resistance and good rigidity. While its long-term use temperature is slightly lower than that of PPS, its heat resistance of approximately 170°C still meets the demands of many high-temperature components. PPA maintains stable and superior rigidity across a wide temperature range, giving it a significant advantage in automotive lightweight design. Additionally, PPA’s high tensile strength, elongation at break, and excellent fatigue resistance further expand its application scope in automotive manufacturing.
Both PPS and PPA exhibit wide applicability beyond the automotive and transportation sectors. They are also extensively used in electronics and electrical engineering, environmental protection, and other fields. In the electronics industry, PPS’s high-temperature resistance, chemical corrosion resistance, and high mechanical strength make it an ideal material for manufacturing electronic device housings, motor components, and electronic connectors. Meanwhile, PPA’s good heat resistance and mechanical properties have led to its widespread use in high-temperature components of electronic devices.
It is worth noting that while PPS and PPA share similar application potential in many aspects, they still exhibit significant differences in chemical structure, heat resistance, mechanical properties, dimensional stability, and flame retardancy. Therefore, when choosing which material to use, specific application needs and performance requirements must be carefully considered. For instance, PPS may be a better choice for applications requiring higher temperature resistance and dimensional stability, while PPA may be more suitable for those needing higher mechanical performance.
In conclusion, PPS and PPA, as two high-performance engineering plastics, are showing promising application prospects in new energy vehicles and various other fields. With continuous technological advancements and the exploration of new applications, these two materials are expected to play an even more important role in the future.