September 27, 2024 – Polyamide, commonly known as nylon, represents a versatile family of thermoplastic linear polymers characterized by their unique repeating amide (-CO-NH-) units. Among its diverse members, nylon 6, nylon 8, nylon 11, nylon 12, nylon 66, nylon 610, and nylon 1010 each bring their own set of attributes to the table. These materials boast high crystallinity, distinct melting points, rigid surfaces, exceptional wear resistance, low friction coefficients, self-lubricating properties, impressive shock absorption, and sound dampening capabilities. Furthermore, they exhibit resistance to low temperatures, moderate heat tolerance, and outstanding electrical insulation. However, their significant water absorption and sensitivity to acids remain notable drawbacks.
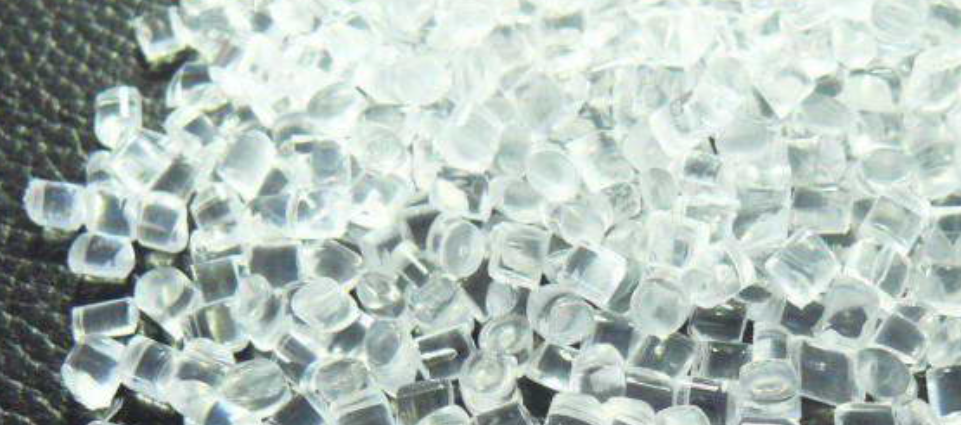
The journey of polyamide began in the early 1930s when research at DuPont Laboratories set the stage for its development. Nylon 6 emerged in 1935 as the first commercial polyamide, swiftly carving a niche in textiles and synthetic fibers. The subsequent decade witnessed the advent of nylon 66, boasting higher melting points and enhanced heat resistance, marking polyamide’s entry into the realm of engineering plastics. This breakthrough facilitated its widespread application in machinery and industrial sectors. Over time, the polyamide family expanded, with newer variants like nylon 11 and nylon 12 finding specialized uses.
In terms of strength and stiffness, polyamide, particularly nylon 66, stands out with its superior tensile strength and modulus, capable of enduring substantial forces and heavy loads. According to Color Masterbatch Industry Network, polyamide’s heat resistance is also noteworthy, with nylon 66 maintaining stable physical and mechanical properties under high temperatures, making it a preferred choice for high-temperature applications.
Moreover, polyamide’s exceptional chemical resistance ensures stability in acidic and alkaline environments. Its low friction coefficient and wear resistance make it invaluable in applications requiring abrasion resistance and lubrication, such as bearings and gears. The material’s fatigue resistance is commendable too, retaining high strength and toughness even under repeated loading and stress cycles.
Interestingly, polyamide’s high moisture absorption finds utility in textiles and fibers, imparting softness, breathability, and moisture-wicking properties to nylon fibers. Additionally, polyamide’s excellent processability, including injection molding, extrusion, and compression, allows for the effortless creation of intricate shapes.
Polyamide’s extensive applications span multiple domains. In textiles and fibers, it is ideal for clothing, socks, bedding, ropes, and more. Within engineering plastics, it facilitates the production of mechanical parts, automotive components, electronic housings, and piping systems. The automotive sector leverages its high strength, heat resistance, and chemical resistance for vehicle parts and assemblies. In packaging, polyamide films and membranes, known for their moisture resistance and durability, are favored in food and electronics packaging. Medical devices and supplies benefit from its biocompatibility and corrosion resistance, making it crucial for medical instruments, surgical tools, catheters, and artificial joints. Lastly, in electronics, polyamide serves as an insulation material, wire and cable jackets, and electronic component holders, playing an indispensable role.