Polyamide (PA), widely known for its remarkable properties such as high strength and excellent heat resistance, has demonstrated extraordinary application value in various fields like textiles, engineering, and automotive, making it an indispensable part of modern industry.
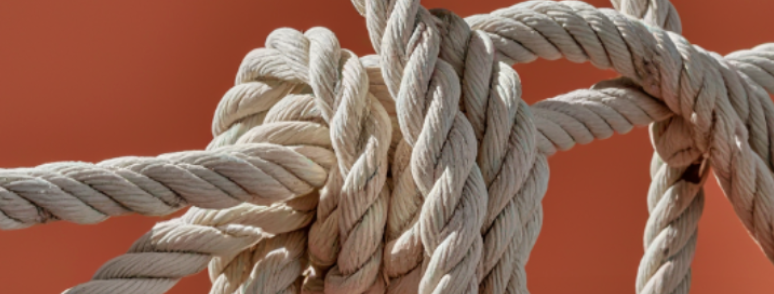
Tracing back the development journey of polyamide, it’s evident that it’s a history filled with innovation and breakthroughs. As early as the 1930s, DuPont Laboratories embarked on polyamide research. In 1935, nylon 6 (polycaprolactam), the first commercialized polyamide material, emerged, marking the beginning of the polyamide era. Nylon 6 achieved huge commercial success, swiftly dominating the textile and synthetic fiber industries. By the 1940s, nylon 66 (polyhexamethylene adipamide) appeared, transitioning into a vital engineering plastic due to its higher melting point and heat resistance, shining brightly in machinery and industrial applications. Since then, the polyamide family has continuously expanded with the emergence of new materials like nylon 11, nylon 12, nylon 610, and nylon 1010, further broadening polyamide’s application areas.
Polyamide’s significant role in multiple fields is intricately linked to its unique characteristics. As a linear thermoplastic polymer, the acylamino (-CO-NH-) structural units on polyamide’s main chain endow it with notable features. For instance, nylon 66, with a tensile strength exceeding 80MPa and a modulus surpassing 3000MPa, stands out as an excellent structural material. Its high melting point of approximately 260℃ maintains its physical and mechanical properties even under high temperatures, making it a preferred material for high-temperature applications like automotive engine components.
Besides high strength and heat resistance, polyamide also boasts a low friction coefficient and superior wear resistance, vital in applications requiring durability and lubrication, such as bearings and gears. Additionally, polyamide’s high hygroscopicity allows it to absorb and release moisture, beneficial in textiles, making nylon and other polyamide fibers soft, breathable, and moisture-wicking.
It’s worth mentioning that flame-retardant nylon, an important polyamide branch, plays a crucial role in areas demanding high fire resistance. With the addition of flame retardants, it significantly enhances oxygen index, reducing combustion risk and fire spread, thus finding widespread use in electronics, building materials, and transportation.
According to the Color Masterbatch Industry Network, polyamide’s applications are extensive. In textiles, nylon’s softness, breathability, and moisture-wicking properties make it ideal for clothing, socks, bedding, and specialty ropes. As an engineering plastic, nylon’s strength, rigidity, heat resistance, and chemical corrosion resistance make it suitable for mechanical parts, automotive components, electronic casings, and piping systems. Its presence is ubiquitous in automobiles, from engine covers to seat components. Additionally, nylon finds important applications in packaging, medical devices, and electronics.
In conclusion, polyamide, with its unique properties and diverse applications, holds a significant position in modern industry and life. With technological advancements and expanding application areas, polyamide is poised for continuous innovation, promising more surprises and conveniences.