December 16, 2024 – In the realm of plastic processing, the significance of plastic modification technology cannot be overstated, as it caters to the diverse needs of various application scenarios. Through a series of innovative techniques, the properties of plastics can be significantly enhanced, thereby broadening their scope of use.
Among the myriad of plastic modification methods, reinforcement and toughening stand out as two prominent approaches. Reinforcement primarily involves the incorporation of fibrous or platelet fillers, such as glass fibers or carbon fibers, into plastics to elevate their rigidity and strength. For instance, the glass fiber-reinforced nylon widely used in power tools is a product of this modification technique. On the other hand, toughening entails adding substances like rubber or thermoplastic elastomers to plastics to boost their toughness and impact resistance. Toughened polypropylene found in automobiles, household appliances, and industrial sectors serves as a typical example.
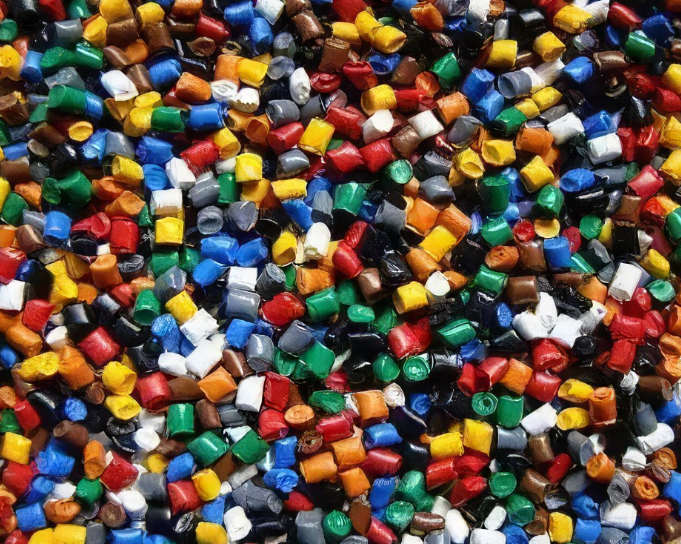
Beyond reinforcement and toughening, blending and alloying are also indispensable techniques in plastic modification. Blending involves the uniform mixing of two or more partially compatible polymer materials to meet specific physical, mechanical, optical, or processing requirements. Alloying, similar to blending, involves better compatibility among components, easily forming a homogeneous system to achieve properties unattainable by a single component. The PC/ABS alloy and PS-modified PPO are quintessential applications of alloy modification.
Furthermore, filler modification is another commonly employed method. By adding fillers to plastics, not only can the physical and mechanical properties of the material be improved, but costs can also be effectively reduced. Additionally, there are other modification techniques, such as utilizing conductive fillers to lower the electrical resistivity of plastics, adding antioxidants or light stabilizers to enhance material weather resistance, incorporating pigments or dyes to alter material color, and adding internal or external lubricants to improve material processability.
It is worth mentioning that apart from these physical modification methods, chemical modification also plays a crucial role. By modifying plastics through chemical reactions, specific properties can be imparted. Examples of chemical modification include maleic anhydride-grafted polyolefins, cross-linked polyethylene, and the use of peroxides in the textile industry to degrade resins for improved flowability and fiber-forming properties.
In summary, plastic modification technology opens up endless possibilities for the plastic processing industry. Through continuous innovation and research and development, we can anticipate the emergence of more high-performance, multifunctional plastic products, bringing greater convenience to people’s lives and industrial production.