December 5, 2024 – As global concern over plastic waste intensifies, plastic recycling has emerged as an unstoppable trend. In response, a growing number of beverage packaging solutions are adopting connected cap designs to minimize cap disposal and enhance recycling efficiency. Notably, the European Union’s Directive 2019/904 mandates that, from July 2024, all plastic bottles with a capacity of up to 3L must have caps attached to the bottle body for production and sale within the EU. This regulation poses new technical challenges for cap manufacturers, plastic bottle producers, and related equipment suppliers.
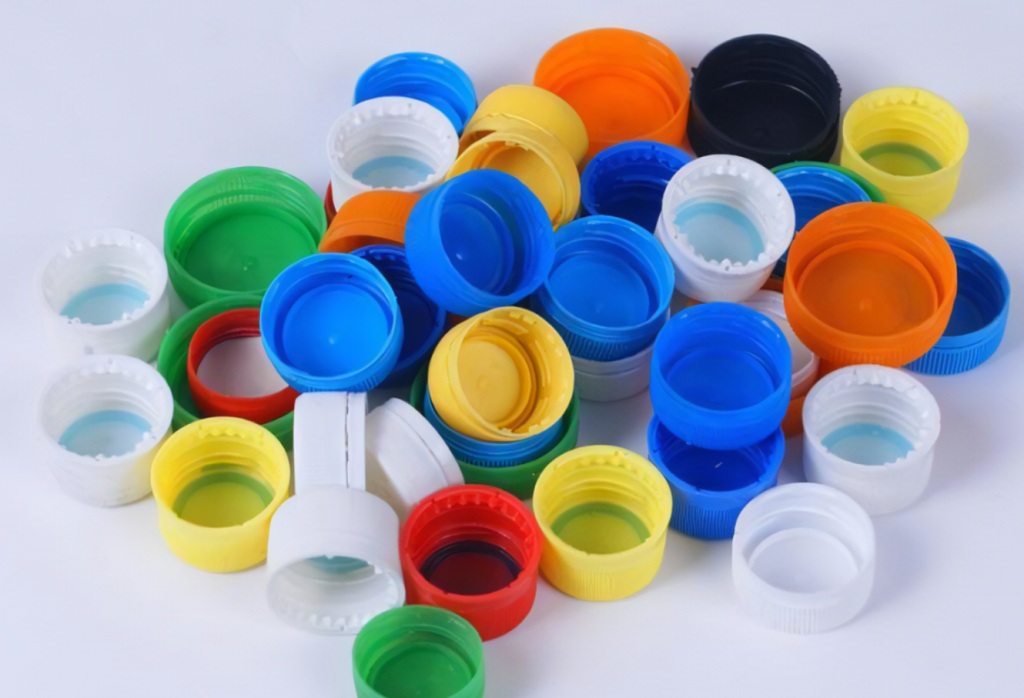
Amidst these clear industry demands, connected caps must not only ensure consumer convenience and product freshness but also avoid increasing production costs or disrupting bottle and neck designs, as well as the operation of filling lines and capping machines. Additionally, these caps need to cater to both lightweight press-on and threaded cap requirements, meeting higher standards for sealing performance.
So, how can the industry meet this wave of demand, particularly regarding the material and coloring of connected caps? According to Color Masterbatch Industry News, the formulation design of color masterbatch for caps is crucial. Plastic bottle caps share common requirements across different beverage products, such as good sealing properties and food safety. During injection molding and application, multiple performance indicators of the color masterbatch must be considered, including heat resistance, warpage, dispersion, migration resistance, and safety.
Firstly, heat resistance is a key factor in cap color masterbatch selection. Given the high melt temperatures during injection molding and the extended residence time in high-temperature barrels, pigments with excellent heat resistance are essential to prevent color changes. Moreover, considering cost and production efficiency, multi-cavity molds are commonly used, further emphasizing the need for heat-resistant colorants.
Secondly, warpage is another critical factor affecting cap sealing performance. Therefore, pigments must be carefully chosen to ensure caps remain distortion-free. Furthermore, dispersion plays a vital role in cap appearance. Poor pigment dispersion can lead to color spots on the product surface, compromising quality.
Migration is also a significant concern. Since plastic caps directly contact food and beverages, any migration issues can result in color cross-contamination and potentially unsafe products. Thus, pigments with potential migration risks must be avoided.
Lastly, safety is a fundamental requirement for color masterbatch used in plastic caps. All raw materials and pigments must comply with relevant food safety regulations and undergo rigorous testing, such as immersion tests. Special caution is needed when selecting sensitive color varieties like blue ultramarine.
In summary, the formulation design of plastic cap color masterbatch must consider multiple factors to ensure that connected caps meet market demands in production and application. As technology advances and markets evolve, we anticipate the emergence of more innovative solutions to drive the sustained development of plastic recycling and environmental protection efforts.