April 11, 2025 – In the arena of high – performance materials, PEEK is emerging as a highly – spotlighted star. PEEK, whose Chinese name is polyetheretherketone, belongs to the polyaryletherketone (PAEK) family. Its molecular structure is formed by the connection of phenylene rings through ether bonds and carbonyl groups, resulting in a crystalline aromatic thermoplastic polymer. This unique molecular configuration endows PEEK with a series of remarkable properties. It is heat – resistant, corrosion – resistant, radiation – resistant, and features high impact strength, excellent wear and fatigue resistance, as well as outstanding processing performance.
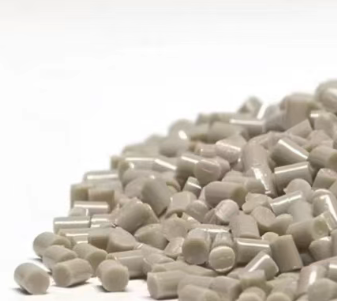
The core performance advantages of PEEK materials are highly prominent. In terms of lightweight and high – strength, its density is only about one – third that of aluminum alloy, yet its specific strength (the ratio of strength to density) is 8 times that of aluminum alloy. This characteristic enables significant weight reduction when manufacturing components. When carbon – fiber – reinforced PEEK (CF/PEEK) is used, its mechanical properties can be further optimized. The tensile strength and modulus are close to those of titanium alloy, while the density is merely 36% of that of titanium alloy. In the fields of high – temperature resistance and wear resistance, PEEK can be stably used in an environment of 250℃ for a long time and can withstand temperatures above 300℃ in the short term. It is especially suitable for high – speed and high – load working scenarios such as robot joints. Meanwhile, its self – lubricating property greatly reduces friction loss and effectively extends the service life of components. Considering its comprehensive performance, PEEK has excellent chemical corrosion resistance, flame retardancy, and insulation properties, so it can completely replace metals in complex environments. Notably, the CF/PEEK composite material has successfully solved the problem of pure PEEK being brittle at low temperatures, achieving a balance between rigidity and flexibility.
According to AsiaMB, with these excellent comprehensive properties, PEEK has been widely applied in numerous fields. In the new – energy vehicle sector, it can be used in key parts such as 800V high – voltage fast – charging enameled wires and motor bearings. The usage of PEEK in the domestic automotive industry has exceeded 520 tons. PEEK also plays a crucial role in the lightweight process of implant – level medical devices and aerospace components. Particularly, in the field of humanoid robots, PEEK shows great application potential. It can be used in robot joints and transmission components. For example, after using PEEK materials, Tesla’s Optimus Gen2 successfully reduced its weight by 10 kg and increased its walking speed by 30%. When CF/PEEK is applied to harmonic reducers, the load – bearing capacity is increased by more than 30%. In six – axis force sensors, using PEEK to replace aluminum alloy effectively reduces inertial mass errors and improves measurement accuracy. Tesla plans to mass – produce 500,000 robots in 2027. Calculated at 195 tons of PEEK required for every 100,000 robots, its long – term market potential can reach the scale of hundreds of billions.
Relevant statistical data shows that from 2017 to 2024, the domestic production of PEEK has soared from the initial 200 tons to 3808 tons, and the demand has also climbed from 700 tons to 3894 tons. In 2024, the PEEK market size in China was approximately 1.9 billion yuan. By 2025, its production capacity is expected to break through the 10,000 – ton mark, demonstrating a strong development momentum.