August 07, 2024 – Since its initial development by the British Imperial Chemical Industries in 1978, PEEK, or polyetheretherketone, has emerged as an outstanding engineering thermoplastic. Widely produced and sold by companies like Victrex under the brand “Victrex PEEK”, this material has gained immense popularity in the industry due to its remarkable mechanical properties, chemical resistance, high thermal stability, and wear resistance.
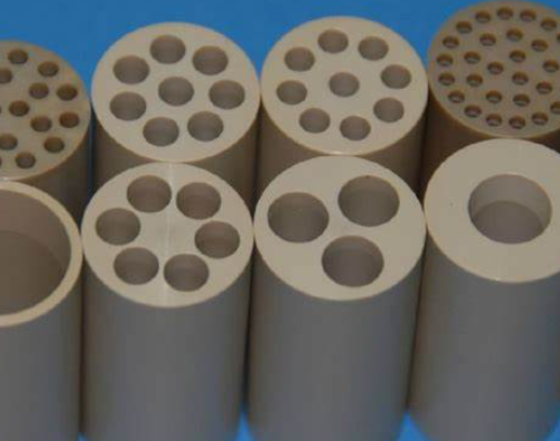
PEEK boasts an exceptional melting point of approximately 343°C, allowing it to withstand continuous use at temperatures up to 250°C, thus ensuring its stability in high-temperature environments. Furthermore, its chemical stability is equally noteworthy, as it can resist various chemicals, including acids, alkalis, and organic solvents. The material also exhibits impressive mechanical strength and rigidity, maintaining its excellent physical properties even at high temperatures.
PEEK’s versatility has led to its diverse applications. In aerospace, it is utilized in manufacturing internal components of aircraft and spacecraft, such as seat supports and cable insulators. In the automotive sector, PEEK finds use in engine parts, transmission, and brake system components. Additionally, due to its good compatibility with human tissue, PEEK is often employed in the production of surgical implants and medical devices in the healthcare industry. It also serves as a high-performance insulating material in various other sectors.
Processing PEEK demands specialized techniques and equipment. Given its high melting point, common processing methods include injection molding, extrusion molding, and machining. Injection molding enables the production of complex-shaped parts, while extrusion molding is primarily used for standard profiles like rods and sheets. Machining, on the other hand, is more suitable for manufacturing high-precision parts and components.
Looking ahead, the application areas of PEEK are poised to expand further with advancing technology. Currently, researchers are exploring combinations of PEEK with other materials to create superior composite materials with enhanced performance. Meanwhile, as the demand for sustainable materials grows, the recycling and reuse of PEEK are becoming focal points of research. Evidently, PEEK is destined to play a more prominent role in environmental protection and sustainable development.
According to the Color Masterbatch Industry Network, PEEK, as a high-performance engineering plastic, holds promising application prospects in multiple fields. With deepening scientific research and technological advancements, PEEK and its composites are expected to occupy a significant position in the future of materials science, offering more innovative and sustainable solutions to various industries.