August 13, 2024 – The quality of color masterbatch products is directly impacted by the dispersion of pigments during the manufacturing process. To address the challenges associated with pigment dispersion, color masterbatch manufacturers are actively exploring various strategies aimed at expanding market share and optimizing cost structures.
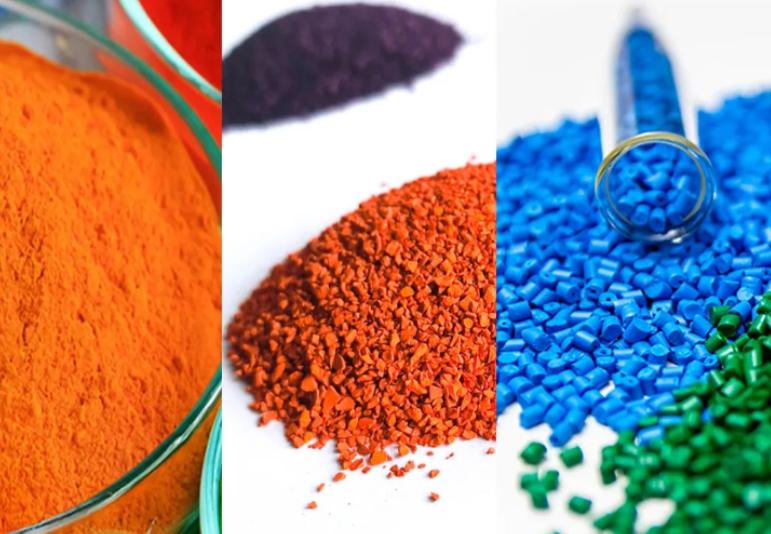
The inherent characteristics of pigments, such as surface activity and intermolecular forces, contribute to the complexity of achieving optimal dispersion. These factors often lead to the aggregation of pigment particles during production, processing, and application, thereby increasing the difficulty of achieving uniform dispersion. However, through refined control of the dispersion process, manufacturers can achieve a homogeneous and stable distribution of pigment particles.
According to AsiaMB, companies have implemented a range of effective strategies to tackle the pigment dispersion challenges. These include the use of advanced dispersion equipment like high-speed mixers and ultra-fine grinding machines, which utilize powerful shearing and impact forces to break up pigment aggregates. Additionally, the introduction of suitable dispersants and additives helps modify intermolecular interactions, reducing the tendency for pigments to clump together and forming a stable dispersion system. Furthermore, optimizing the production process flow is crucial to enhancing pigment dispersion.
In the modern color masterbatch manufacturing industry, the application of “wetting” theory aims to achieve superior dispersion results. However, due to the diverse range of pigments and limitations in production techniques, even products from the same batch can exhibit variations in quality. This complexity increases the difficulty of raw material selection for masterbatch factories, raises coloring costs, and affects overall competitiveness.
The industry has been continuously exploring ways to enhance pigment dispersion and color stability. Innovative technologies, such as the pre-formulation techniques introduced by CIBA and Sun Chemical, have significantly improved pigment dispersion performance.Recently, new pigment preformulations using PP wax and PE wax as carriers have emerged. These products utilize the shear force transmission characteristics of resin melts to achieve efficient dispersion, offering a novel solution for the industry.
In terms of color masterbatch preparation strategies, the mainstream methods include direct preparation using pigment powders, dilution with high-concentration monochromatic masterbatches, and production with pre-dispersed pigment technology. Each method has its advantages and limitations, requiring careful selection based on specific needs and conditions. Meanwhile, as environmental and safety standards continue to rise, color masterbatch manufacturers need to increase their investment in environmental protection, create a green production environment, and promote automation and large-scale production.
In conclusion, by integrating advanced dispersion equipment, suitable dispersants and additives, and optimizing the production process flow, manufacturers can effectively address pigment dispersion challenges. This lays a solid foundation for the high-quality production of color masterbatch and other products, driving the sustained development of the color masterbatch industry.