January 24, 2025 – Tackling Common Issues in Plastic Processing: Peeling and Water Spots
In the plastic processing industry, peeling phenomena remain a persistent issue, not only detracting from the visual quality of products but also posing significant challenges for manufacturers. According to industry insiders, peeling often arises from the mixing of two carrier resins with vastly different properties and poor compatibility between them. This incompatibility is akin to mixing oil and water in a bottle, where eventual separation is inevitable.
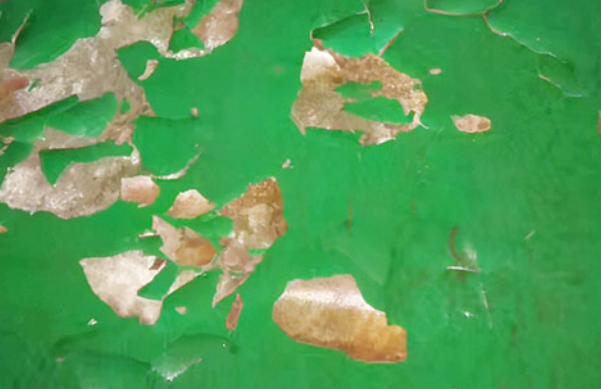
When using a single plastic material, peeling can occur due to external forces causing incompatibility between the carrier in the color masterbatch and the processing resin. To address this, experts in the field suggest several strategies: switching to a color masterbatch with the same carrier, minimizing the carrier resin content in the color masterbatch to increase its concentration, or even replacing the carrier resin in the color masterbatch to reproduce it.
Another prevalent issue in plastic processing is water spots with patterns. AsiaMB has learned that there are four primary causes for this problem. Firstly, moisture in the color masterbatch or the resin used by the customer can lead to water spots. Secondly, an insufficient length-to-diameter ratio of the extruder or inadequate mixing in the kneading section can result in uneven dispersion of the color masterbatch. Thirdly, poor dispersion within the color masterbatch itself can be a factor. Lastly, using a color masterbatch that is too concentrated with too little addition can also cause this issue.
In response to these problems, industry experts have proposed a range of solutions. For color masterbatches or resins containing moisture, thorough drying is essential. When the extruder’s length-to-diameter ratio is insufficient or the mixing process is inadequate, adjusting extruder parameters or improving the mixing technique can help. For color masterbatches with poor dispersion, opting for higher-quality products is recommended. Lastly, for cases where the color masterbatch concentration is too high and the addition amount too low, adjusting the addition rate of the color masterbatch can ensure product quality and stability.