October 25, 2024 – Plastic’s Ascendancy in Modern Industrial Applications: A Focus on Transparent Plastics
In the relentless pursuit of enhanced material performance for modern industrial and daily products, plastics have emerged as a formidable contender, steadily replacing glass, particularly in optical instruments and packaging. This transition is primarily attributed to plastics’ advantages, including lightweight, excellent toughness, ease of molding, and cost-effectiveness. However, transparent plastics must meet stringent requirements such as high transparency, robust strength, wear resistance, impact resistance, and heat resistance. Achieving these necessitates meticulous adjustments across various stages, including material composition, injection molding processes, equipment, and molds. This article delves into the characteristics and injection molding techniques of three prevalent transparent plastics: PMMA (Polymethyl Methacrylate), PC (Polycarbonate), and PET (Polyethylene Terephthalate).
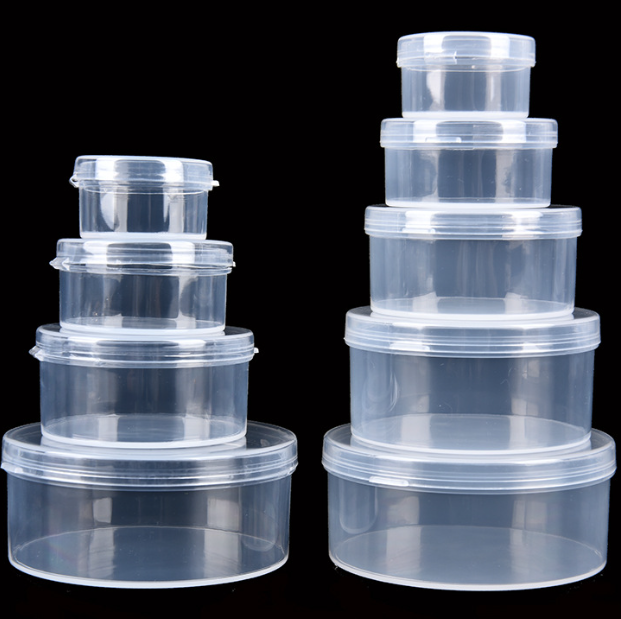
Transparent plastics must first and foremost exhibit high transparency while also possessing good strength, wear resistance, impact resistance, and heat resistance. Among numerous transparent plastics, PMMA, PC, and PET are favored due to their respective superior properties. According to Color Masterbatch Industry News, despite PC being an ideal choice, its higher raw material cost and more complex injection molding process often lead to PMMA dominating practical applications. Conversely, PET’s exceptional stretching capabilities make it widely used in packaging and container sectors.
The injection molding of transparent plastics demands impeccable surface quality, with zero tolerance for defects such as streaks, pores, whitening, haze, black spots, discoloration, or poor gloss. This imposes stringent requirements on raw materials, equipment, molds, and even product design. Transparent plastics often feature high melting points and poor fluidity, necessitating precise adjustments to process parameters like barrel temperature, injection pressure, and injection speed. These adjustments ensure that products can fully fill the mold without deforming or cracking due to internal stress.
Raw material preparation is crucial, necessitating clean and dry materials to prevent impurities and moisture from affecting product transparency. Sealing must also be emphasized during storage, transportation, and feeding. Equally important is the cleanliness of equipment and molds, as any residual old material or impurities in screw and accessory recesses can degrade product quality.
Mold design must also fully consider transparent plastics’ characteristics. For instance, wall thickness should be uniform, with sufficient draft angles; transitions should be gradual and smooth, avoiding sharp corners and edges; gates and runners should be as wide and short as possible, with gate positions strategically set based on the shrinkage and condensation process. Additionally, mold surfaces should be smooth with low roughness, and adequate vent holes and slots should be provided to expel air and melt gases.
In terms of injection molding techniques, specialized screws and injection molding machines with independently controlled nozzle temperatures should be used. Injection temperature, pressure, and speed should be selected based on the plastic resin’s properties. Hold time and cycle time also need to be adjusted according to specific products to minimize internal stress and surface defects. Screw speed and backpressure should be kept within a reasonable range to prevent plastic degradation.
Besides these commonalities, different types of transparent plastics exhibit unique processing characteristics. For example, PMMA has high viscosity and poor fluidity, requiring elevated material temperature and injection pressure. PC also has high viscosity and a high melting point, necessitating high-temperature injection molding and minimized hold time. PET, on the other hand, requires high-temperature injection molding and hot runner molds to elevate mold temperature.
Lastly, defects in transparent plastics, such as silver streaks, bubbles, and poor surface gloss, must be addressed with corresponding solutions. Silver streaks can be eliminated through annealing or optimizing injection molding techniques and mold design. Bubbles can be avoided by enhancing ventilation, optimizing gate design, and increasing mold temperature.
In conclusion, transparent plastics’ applications in modern industrial and daily products are expanding. However, meeting high transparency and other stringent requirements still necessitates meticulous adjustments and optimizations across multiple stages.