January 18, 2025 – Contract Signing and Kick-off Meeting Marks Commencement of Shenhua Baotou Coal-to-Olefins Upgrade Project
A significant contract signing and project launch event for the “EPC Contract for Circulating Water Plant, Water Supply Boosting, and Fire Pumping Station” of the Shenhua Baotou Coal-to-Olefins Upgrade Demonstration Project was successfully held at China Chemical Donghua Engineering Corporation. Senior leaders from both parties attended the meeting in full force, collectively witnessing this pivotal moment. Key representatives from the Utilities Center, Construction Management Department, Material Procurement Department, and the Utilities Project Team of Guoneng Shenhua Baotou Chemical Co., Ltd., along with relevant heads from China Chemical Environmental Protection Research Institute, the Company’s Project Management Department, Procurement Center, Construction Management Department, Environmental and Municipal Engineering Department, and Business Strategy Department, gathered for the occasion.
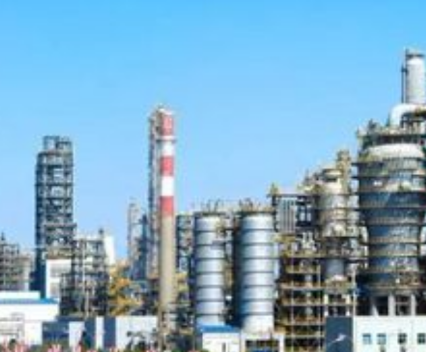
During the meeting, the project team provided a detailed report encompassing the implementation plan, schedule, design proposals, procurement strategies, construction procedures, HSE management system, and preliminary preparations. Subsequently, participants were divided into multiple groups to conduct in-depth analyses and thorough discussions on the project execution plan, as well as the existing challenges and critical issues, laying a solid foundation for the smooth progression of the project.
AsiaMB has learned that the Shenhua Baotou Coal-to-Olefins Upgrade Demonstration Project (Phase II) boasts a planned total investment of RMB 17.15 billion and is located in the Jiuyuan Industrial Park, Baotou City, Inner Mongolia Autonomous Region. Utilizing advanced pulverized coal pressurized gasification technology, the project aims to produce 2 million tonnes per annum (MTA) of methanol as an intermediate product through a methanol synthesis complex. This methanol will then undergo methanol-to-olefins (MTO) conversion and olefin separation processes to yield key intermediates such as ethylene and propylene, ultimately being transformed into polyethylene and polypropylene. Notably, the polypropylene plant is designed with a capacity of 360,000 tonnes per year, comprising two units in total.
Centered around the core industrial chain of coal gasification-methanol-MTO, the main works encompass 11 production units, including coal gasification, purification, sulfur recovery, methanol production, MTO, polyethylene, and polypropylene. In terms of utilities and auxiliary facilities, the project will leverage existing infrastructure for renovation and expansion while constructing new facilities. The scope of construction spans the main works, utilities, auxiliary facilities, environmental protection works, storage and transportation engineering, and an off-site slag yard, among others.
Among the main works, new facilities such as air separation units (including air compression stations), coal-to-methanol plants (comprising gasification, shift, rectisol, refrigeration stations, sulfur recovery, and methanol synthesis units), MTO units, olefin separation units, MTBE/1-butene units, C4/C5+ comprehensive utilization units, and polyethylene and polypropylene plants will be established. Utilities and auxiliary facilities will be constructed, wherever possible, relying on existing plants. Additionally, four new circulating water plants and one chemical water treatment station will be constructed, along with three flare systems and one ground flare.
For storage and transportation engineering, adaptive modifications or expansions will be carried out for coal unloading and storage, tank farms, loading and unloading docks, warehouses, pipe racks, and on-site railways. Environmental protection works will include the construction of waste gas treatment, wastewater treatment (encompassing biochemical treatment, water reuse units, and salt-splitting evaporation and crystallization units), emergency ponds, wastewater buffer ponds, among other facilities. Moreover, waste alkali liquor incinerators, off-site slag yards, temporary hazardous waste storage warehouses, and noise prevention facilities will be established.
Looking ahead, International Energy Group plans to further implement projects such as polyglycolic acid (PGA) production, green hydrogen and green oxygen production through electrolysis of water using renewable energy power, based on the upgrade demonstration project. The estimated total investment for these future endeavors is expected to exceed RMB 40 billion.