April 3, 2025 – Kuraray Co., Ltd. has recently announced the discontinuation of its Vecstar™ FCCL (Flexible Copper Clad Laminate) production, while its facility in Saijo, Japan, will continue to focus on manufacturing and expanding the application scope of Vecstar™ Liquid Crystal Polymer (LCP) films. Notably, Vecstar™ stands as the world’s first LCP film, developed through Kuraray’s unique film-forming technology.
Although LCP was once heralded as a promising antenna material for the 5G era, with the potential to surpass polyimide, its widespread adoption has been hindered by several factors. These include the complex and costly manufacturing process of its substrate products, coupled with slower-than-expected downstream commercialization. In recent years, advancements in wireless communication technology have spotlighted electronic components required for high-performance micro/millimeter-wave communication devices. These components, prized for their high power output, gain, low noise, and high linearity, have garnered significant attention from experts in radar and antenna design, as well as electronic warfare. However, the development of such high-performance microwave devices remains constrained by substrate material limitations.
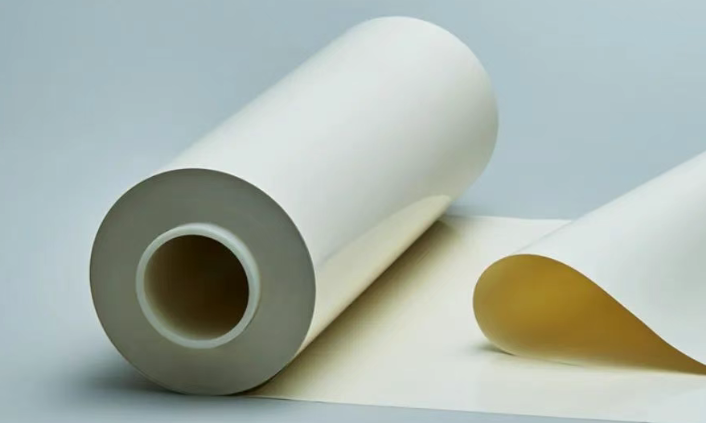
According to AsiaMB’s industry insights, before the advent of LCP substrates, flexible dielectric substrate materials were predominantly polyester and polyimide (PI) resin-based substrates. Among these, PI has long dominated the flexible copper clad laminate dielectric material market, boasting over 80% market share, thanks to its superior heat resistance, flexibility, physical strength, and low dielectric constant (Dk)/dissipation factor (Df). Nevertheless, PI materials pose long-term application risks, particularly their high moisture absorption rate of over 2%, which can drastically alter dielectric properties, affecting signal transmission stability at high frequencies and significantly increasing losses—a critical flaw for antenna and other signal transceiver modules. In contrast, LCP exhibits an extremely low moisture absorption rate (just 0.04% at 23°C over 24 hours), positioning it as a key dielectric layer material to replace PI, especially in 5G communication antennas.
Despite LCP’s properties aligning well with the requirements of core components in high-frequency communications, its unique anisotropic and chemically inert nature presents processing challenges. LCP’s anisotropy means its physical characteristics vary in different directions, while its chemical inertness results in weak copper adsorption, complicating further processing, particularly in multilayer manufacturing. To address these challenges, researchers have proposed using plasma gas to activate LCP, enhancing adhesion and surface activation. Currently, industrial practices often rely on pure adhesive bonding to improve the interlayer bonding between LCP substrates and copper layers. However, plasma treatment followed by adhesive-free direct lamination requires high hot-pressing temperatures, typically 220°C or higher, exceeding the capabilities of standard rapid presses. Additionally, the cost of LCP flexible circuit boards significantly restricts their large-scale application, with LCP radio frequency antennas costing approximately 10-20 times more than their PI counterparts for similar scales.
Beyond flexible circuit boards, LCP finds applications in communication areas such as base station antenna elements and high-speed connectors. Recently, Kingfa Science and Technology’s “2024 Annual Action Plan Evaluation Report for Quality and Efficiency Improvement and Return Enhancement” revealed that the company’s LCP has been widely adopted in components like high-speed connectors, high-speed cooling fans, and new energy battery structural parts. In 5G antenna element design, LCP’s low dielectric loss makes it a preferred alternative to materials like PPS. Furthermore, LCP holds promising prospects in various sectors, including electronics, automotive, and aerospace. In electronics, it can be used for high-density connectors and bobbin frames; in automotive applications, for components in combustion systems; and in aerospace, for radar antenna shields.