January 24, 2025 – The Crucial Role of Production Techniques and Equipment in Masterbatch Manufacturing
Masterbatch, an essential additive in synthetic materials such as plastics and rubbers, plays a pivotal role in determining the quality and application effects of these materials. Currently, the production processes for masterbatch are mainly divided into two categories: wet and dry methods, both of which are continually evolving.
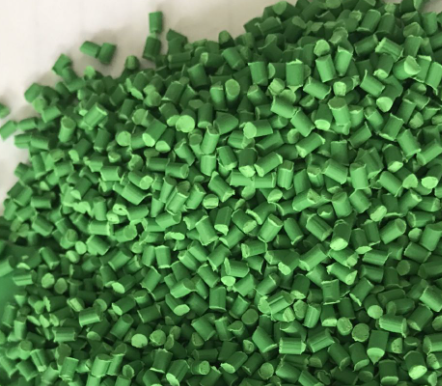
The wet process is a significant method in masterbatch production, involving multiple steps such as grinding, phase inversion, washing, drying, and granulation. Among these, grinding the pigments is a crucial step, requiring a series of technical tests to ensure the fineness and dispersion performance of the pigment particles. The wet process can be further subdivided into four specific methods: ink method, rinsing method, kneading method, and metal soap method. Each method has its unique advantages and applicable scenarios. For instance, the ink method involves three-roll grinding and two-roll plasticizing before extrusion and granulation, while the rinsing method uses sand milling and phase transfer to transfer the pigment into the oil phase, followed by drying and extrusion granulation to obtain the masterbatch.
According to AsiaMB, the dry process is another important method for producing masterbatch, particularly suitable for high-grade products. In the dry process, companies usually prepare pre-dispersed pigments and then mix them with carrier resins using equipment such as high-speed mixers and internal mixers. Finally, the mixture is extruded and granulated to obtain the masterbatch. To improve pigment dispersion, some companies also grind the carrier resins into powder to further enhance product quality.
In terms of equipment, grinding machines, high and low-speed kneaders, mixers, and extrusion granulators are all indispensable in masterbatch production. Grinding machines such as sand mills and cone mills are used for pigment grinding; kneaders ensure stable pigment dispersion through vacuum decompression, volatile extraction, and dehydration; mixers are used for mixing pigments and carrier resins; and extrusion granulators extrude the mixed material into granular form for subsequent processing and use.
With the continuous development of the synthetic material industry in China, the application fields of masterbatch are also expanding. From general plastics to general engineering plastics, special engineering plastics, and thermoplastic elastomers, masterbatch plays a vital role. In the future, functional masterbatch will increasingly be favored by the market, and there is a huge market space for fiber dope coloring. Therefore, we should vigorously develop high-tech functional masterbatch varieties to promote the steady development of the masterbatch industry.