October 12, 2024 – A significant milestone was achieved at 6 p.m. on October 10th within the framework of the 2×450,000 tons/year polypropylene plant project, as the steel truss structure of its three-dimensional warehouse was successfully lifted into its predetermined position.
Boasting a coverage area of 10,860 square meters, the warehouse stands out with its unique truss structure, measuring 60 meters by 90.5 meters, and reaching a column top height of 36.5 meters. With a structural span of 60 meters and a total weight of approximately 431.5 tons, this project undoubtedly ranks among the largest of its kind in the domestic polypropylene sector. Notably, Daxie Petrochemical marked a first in its field by successfully employing hydraulic lifting technology during the steel truss elevation of the three-dimensional warehouse. This technology, combining a core-piercing hydraulic lifter with flexible steel strands, ensured a synchronized, safe, and reliable lift of the entire steel truss structure, offering advantages such as easy transportation and installation, and eliminating the need for intermediate splicing.
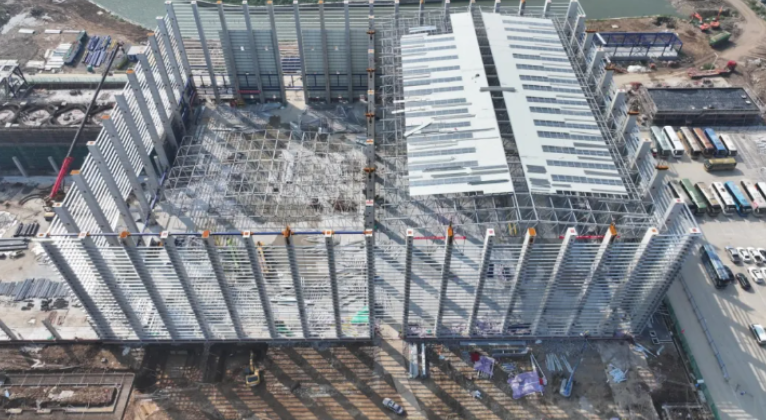
Throughout the construction of the packaging warehouse, Daxie Petrochemical remained grounded in the site’s specific conditions, adopting a problem-oriented approach and actively introducing advanced construction concepts. By tackling various challenges through a multi-faceted strategy, the company continuously optimized and refined the construction plan. The warehouse incorporated an innovative construction technique: “ground modular unit assembly + synchronous hydraulic lifting of ultra-large components + in-air rod supplementation for supports.” This not only effectively controlled costs but also significantly enhanced construction safety, ensuring a smooth and reliable lifting process.
According to Color Masterbatch Industry Network, the project team adopted a multi-point lifting method during the hoisting process. Twelve lifting machines were divided into four groups, arranged in a 2-4-4-2 layout, providing stable lifting force from the east, south, west, and north. This ensured a smooth lift of the steel truss. Additionally, leveraging a modern hoisting equipment control system, functions such as fully automatic synchronous movement, load balancing, attitude correction, and fault alarm were realized through travel and displacement sensing monitoring and computer control. Precise control and adjustment of multiple or single hydraulic lifters were achieved via local controllers, with an adjustment accuracy reaching the millimeter level, thus enabling precise hoisting.
Daxie Petrochemical’s successful application of hydraulic lifting technology not only laid a solid foundation for the smooth progression of the current project but also provided valuable experience for subsequent similar engineering endeavors. Looking ahead, Daxie Petrochemical will continue to commit to the innovation of management concepts, enhance the new driving force of innovation, and steadfastly advance the processes of digitization, automation, and intelligence, thereby continuously injecting momentum into the upgrading and high-quality development of the green chemical industry.