March 6, 2025 – Toray Industries of Japan has made significant strides in the recycling of nylon 66.
The company has recently unveiled an innovative depolymerization technology that utilizes subcritical water to efficiently and uniformly break down nylon 66 resin into its monomer components within just a few minutes, enabling its reuse as raw materials. Subcritical water, existing in a high-temperature and high-pressure state just below the critical point of water (705℉), exhibits properties vastly different from those of water at ambient conditions, such as the ability to dissolve and hydrolyze organic compounds.
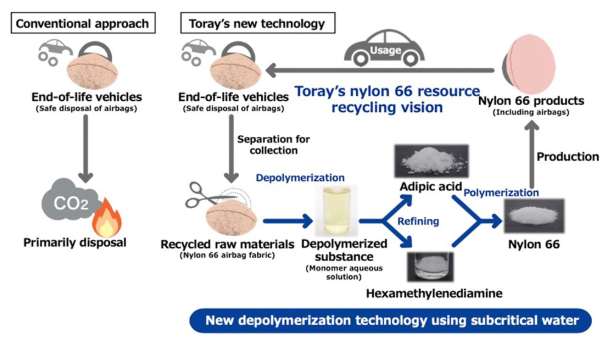
According to AsiaMB’s insights, the annual demand for nylon 66 in Japan is approximately 100,000 tons, while global demand soars to 1.3 million tons. Renowned for its exceptional heat resistance and strength, nylon 66 finds widespread application in the automotive and industrial sectors, including airbags and tire cords in automotive textiles, as well as radiator tanks, cylinder head covers, and oil pans in plastic components. With Japan’s increasingly stringent regulations on automobile and other plastic recycling, used nylon 66 airbags have emerged as a “hot material” for chemical recycling.
Toray states that a demonstration project for the chemical recycling of nylon 6 is already underway, primarily recovering caprolactam monomers. In contrast, the chemical recycling process for nylon 66 is relatively complex, requiring the recovery of hexamethylenediamine and adipic acid monomers. Leveraging its extensive expertise in nylon 6 chemical recycling technology, Toray has thoroughly assessed the depolymerization reaction of nylon 66 in subcritical water and successfully developed proprietary technology that effectively suppresses side reactions, enabling efficient recovery of these two monomers and their re-polymerization into nylon 66.
Toray reveals that its initial plans focus on automotive materials, developing technologies to separate other materials from used equipment such as airbags, as well as techniques for depolymerizing nylon 66 and purifying the separated monomers. This year, the company aims to establish a framework to verify the quality of recycled materials through sample work and assess customer demand. Simultaneously, Toray is actively preparing for large-scale production around 2030, in anticipation of stricter plastic recycling regulations.
Furthermore, Toray pledges to develop comprehensive recycling technologies for both nylon 6 and nylon 66, and plans to expand its chemical recycling expertise from apparel and automotive materials to other industrial applications, contributing to the promotion of a circular economy and the achievement of carbon neutrality goals.