November 27, 2024 – The rise of EVA foam sole materials in the casual athletic footwear industry has been remarkable due to their lightweight and comfortable features. However, EVA’s inherent limitations in flexibility, compression resistance, and slip resistance have prompted the industry to seek improvements through elastomer modification. Among these, SEBS (Styrene-Ethylene-Butylene-Styrene) is emerging as a preferred material, gaining substantial market attention.
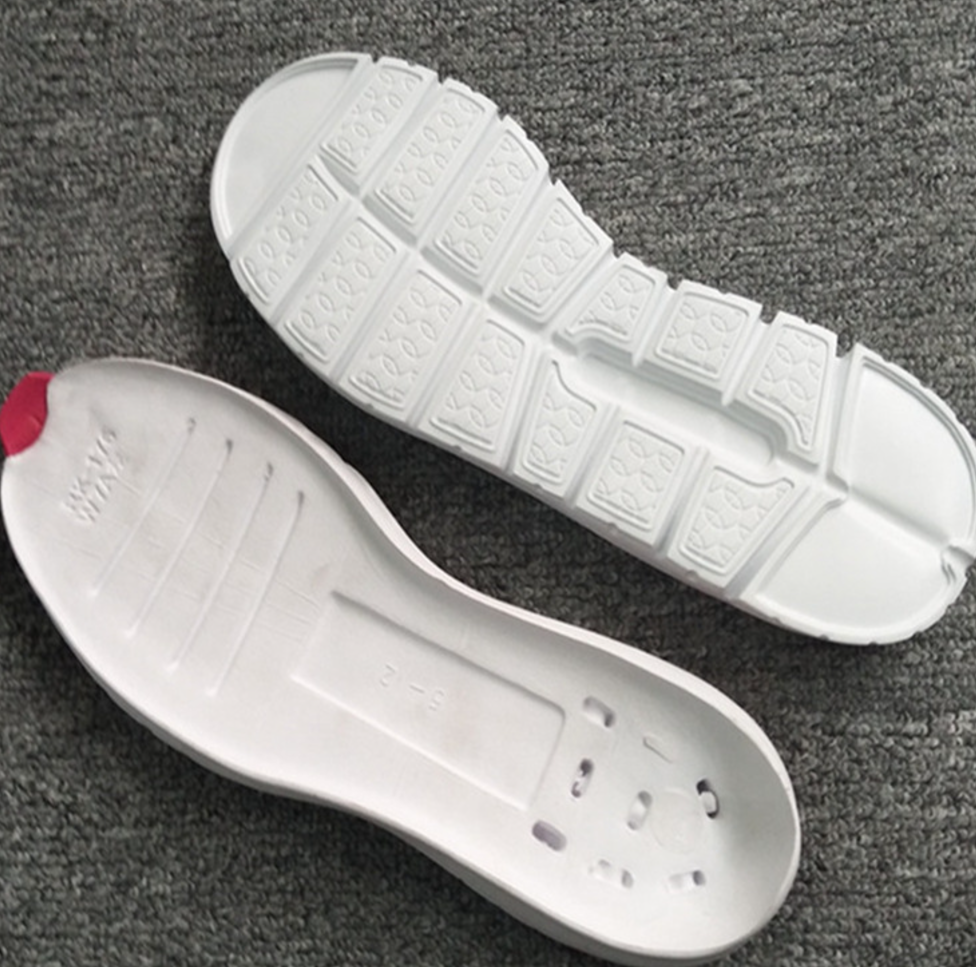
The incorporation of SEBS in the modification process of EVA foam significantly enhances the material’s properties. By fine-tuning the ratio of SEBS to extender oil, manufacturers can produce foam products with optimal softness, hardness, and overall performance. This innovation not only diversifies the EVA foam material product line but also offers consumers a wider array of choices.
In the foaming system, DCP/AC foaming agents are favored for their high decomposition temperature and prolonged gas release. According to Color Masterbatch Industry News, additives are commonly used to regulate the decomposition temperature of AC. When the ratio of AC to ZnO/ZnSt reaches 10:1, with a ZnO to ZnSt ratio of 1:5, the peak decomposition temperature of AC aligns closely with that of DCP, ensuring stable foaming.
Mechanical performance tests reveal that the material’s properties change with extended foaming time at specific temperatures. Density, a crucial indicator of foam materials, varies depending on the foaming process. By adjusting this process, foam materials with densities ranging from 0.15g/cm3 to 0.49g/cm3 can be produced, catering to diverse application needs.
The amount of SEBS used significantly impacts the performance of EVA foam. As SEBS content increases, material hardness and tensile strength decrease, while tear strength remains relatively stable. Elongation at break initially rises and then slightly declines. This behavior is attributed to the rubber segments in SEBS imparting good elasticity, while the plastic segments act as physical cross-linking points. Notably, different SEBS grades affect foam performance differently, even at the same usage level.
Furthermore, SEBS addition influences the foam’s cell structure. Without SEBS, the cells are small and unevenly distributed. With SEBS, cells become larger, more fully developed, and uniformly distributed. Both the amount and grade of SEBS impact cell size and uniformity, providing new insights into optimizing foam structure.
In terms of melt viscoelasticity, SEBS also plays a significant role. As cross-linking density increases, the melt’s elastic modulus rises more sharply, favoring the formation of tight cell structures. The amount and grade of SEBS affect the melt’s viscoelasticity and cross-linking density, subsequently influencing the foam’s performance.
In summary, SEBS, as a vital modifier for EVA foam materials, significantly impacts performance, cell structure, and melt viscoelasticity. As technology advances and the market expands, the prospects for SEBS application in the EVA foam material sector look increasingly promising.