October 19, 2024 – A significant milestone has been achieved in the construction of a large-scale polypropylene plant project in China, as the steel grid structure of its three-dimensional warehouse has been successfully lifted into place. This marks a steady progression towards the next phase of the project’s development.
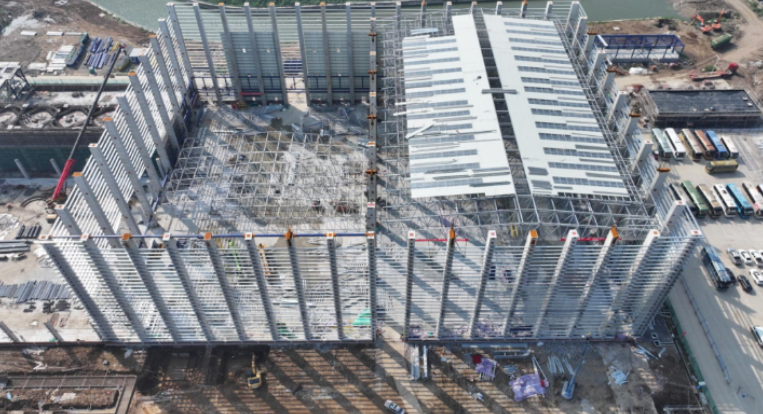
The roof of this three-dimensional warehouse boasts an advanced grid structure, spanning an impressive 10,860 square meters. With dimensions of 60 meters by 90.5 meters and a column height of 36.5 meters, the structure’s span reaches 60 meters, and its overall weight is approximately 431.5 tons. This scale sets it apart as a leader among similar polypropylene projects in the country. The successful integral lifting of the steel grid structure represents Daxie Petrochemical’s first adoption of hydraulic lifting technology, which has proven to be a resounding success.
According to Color Masterbatch Industry News, the hydraulic lifting technology utilizes a core device known as a hydraulic lifter with a through-core structure, paired with flexible steel strands as load-bearing cables, to achieve synchronous lifting of the entire steel grid structure. This technique is not only safe and reliable but also offers unique advantages such as lightweight load-bearing components, ease of transportation and installation, and the elimination of additional splicing during the process.
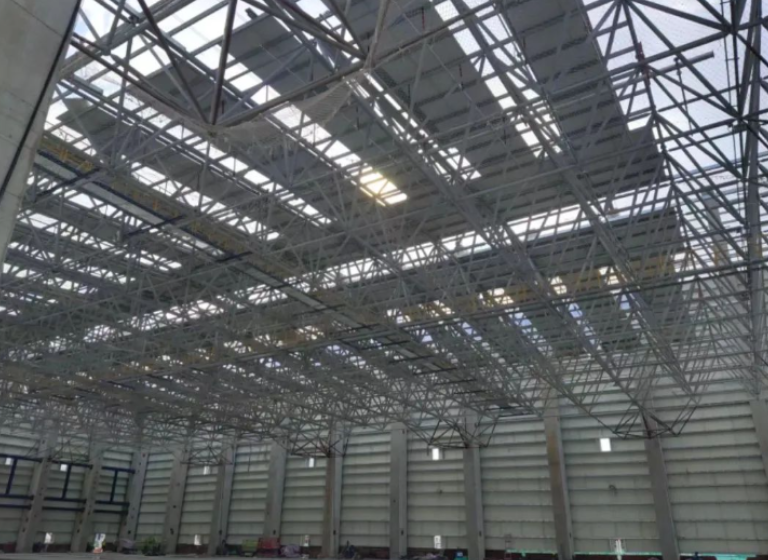
Throughout the construction of the three-dimensional warehouse, Daxie Petrochemical has consistently adhered to a foundation based on the construction environment, guided by practical issues, and led by advanced construction thinking. Through multiple innovative measures, they have successfully overcome numerous challenges and continuously optimized and improved the construction plan. They have adopted an advanced construction process of “ground module unit assembly + synchronous hydraulic lifting of ultra-large components + in-air reinforcement of supports,” which effectively controls costs while significantly enhancing construction safety and ensuring the stability and reliability of the entire lifting process.
During the lifting operations, Daxie Petrochemical employed a multi-point lifting method, dividing 12 lifting machines into four groups with a 2-4-4-2 layout distributed in the east, south, west, and north directions. This provided stable lifting power for the steel grid structure. Additionally, they relied on a modern lifting equipment control system, utilizing travel and displacement sensor monitoring and computer control technology to achieve precise control over the lifting process. This system can automatically perform various functions such as synchronous movements, load balancing, attitude correction, and fault alarms, and it allows for millimeter-level precise adjustments to multiple or single hydraulic lifters through local controllers, ensuring the accuracy of the lifting.
The successful application of hydraulic lifting technology not only lays a solid foundation for the smooth progression of the current project but also accumulates valuable experience for Daxie Petrochemical’s subsequent similar engineering endeavors. Looking ahead, Daxie Petrochemical will continue to deepen its innovative management concepts, strengthen the new driving force of innovation, and steadfastly advance the digital, automated, and intelligent transformation and upgrading. This will provide continuous momentum for the upgrading and high-quality development of the green chemical industry.