March 23, 2025 – Covestro announced that the modernization of its TDI (toluene diisocyanate) plant in Dormagen has been successfully completed and officially put into operation. It is reported that the highlight of this renovation was the installation of a new reactor weighing 150 tons and nearly 20 meters high. This reactor achieves efficient energy recycling by capturing energy generated during the reaction process for steam production. According to sources from the Color Masterbatch Industry Network, the energy consumption of the renovated plant has been reduced by 80% compared to traditional processes, resulting in an annual reduction of 22,000 tons of carbon dioxide emissions, significantly improving energy efficiency and environmental performance.
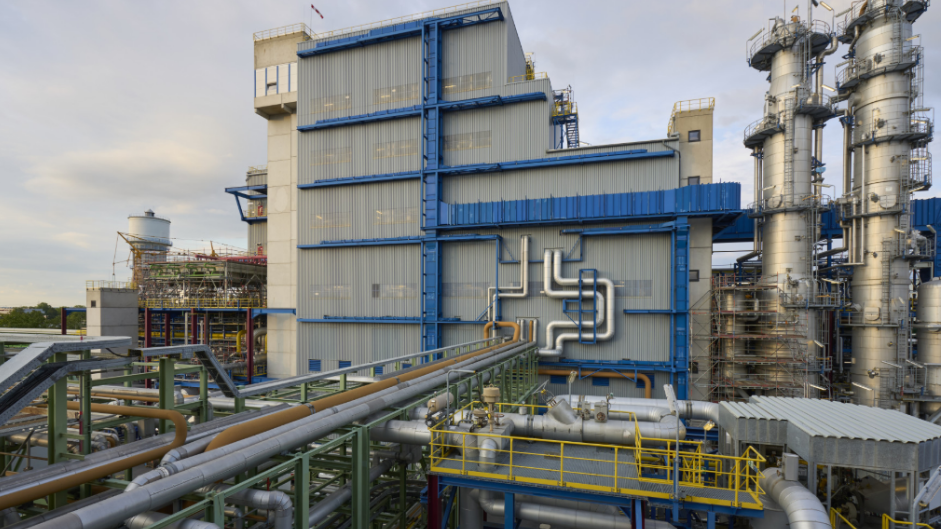
As Covestro’s largest TDI production base in Europe, the plant has an annual production capacity of 300,000 tons and utilizes Covestro’s proprietary gas-phase technology. Since the renovation began in the summer of 2023, Covestro has invested millions of dollars. The successful completion of this renovation not only solidifies the plant’s market position amid rising energy costs but also significantly enhances the overall competitiveness of TDI production in Europe, while providing customers with high-quality TDI products with a lower carbon footprint. As a key raw material for polyurethane-based materials, the green production of TDI is of great significance to the entire industry chain.
Amid the global trend of green transformation in the TDI industry, China has also made significant progress. In August 2024, Shaanxi Coal Technology Center successfully developed the world’s first pilot plant for non-phosgene TDI green synthesis process technology, marking a solid step forward in China’s journey towards low-carbon and green TDI production. Meanwhile, global companies are promoting the low-carbonization of isocyanates through various means such as process innovation, raw material substitution, and breakthroughs in carbon recycling. For example, Levima New Material announced its domestically pioneered non-phosgene XDI production technology and obtained customer validation. The Institute of Process Engineering of the Chinese Academy of Sciences, in collaboration with the Shaanxi Coal team, completed the industrialization test of urea-based non-phosgene MDI technology, breaking international monopolies. Additionally, as a key raw material for bio-based polyurethanes, the market scale of bio-based MDI is gradually expanding under the dual carbon background, with companies like BASF, Covestro, Huafon Chemical, and LANXESS all making layouts in this area.
Influenced by energy costs and environmental policies, overseas TDI production capacity continues to shrink, and global capacity is gradually concentrating in China. With its well-established industrial chain, China has become the main global supplier of TDI, accounting for nearly 40% of global TDI production capacity. However, the existing and planned domestic production capacities still mainly rely on the phosgene process, and the large-scale application of low-carbon technologies has become the key to future development. From a market perspective, since the beginning of the year, the domestic TDI market has remained stable, but downstream demand has been lackluster, resulting in net profit losses for most TDI producers. With the restructuring of the global production capacity landscape, while ensuring supply, China needs to accelerate technological upgrades to address the dual challenges of international competition and low-carbon transformation. The upgrade of Covestro’s European plant not only sets an energy efficiency benchmark for the industry but also signifies that TDI production is transitioning from a traditional high-energy-consumption model to a green and efficient one, injecting new momentum into the sustainable development of the polyurethane industry.