January 23, 2025 – Teijin Group Announces Closure of Arnhem Aramid Fiber Production Site as Part of Cost-Saving Measures
Teijin Group, through its subsidiary Teijin Aramid, has recently announced the closure of its aramid fiber production facility in Arnhem, the Netherlands, as part of a series of cost-saving measures. Amidst intensifying global competition, particularly from Asian markets, Teijin Aramid believes these measures are crucial for the company’s sustained development. Currently, Teijin Group operates three production plants in the Netherlands, two in Japan, and one in Thailand.
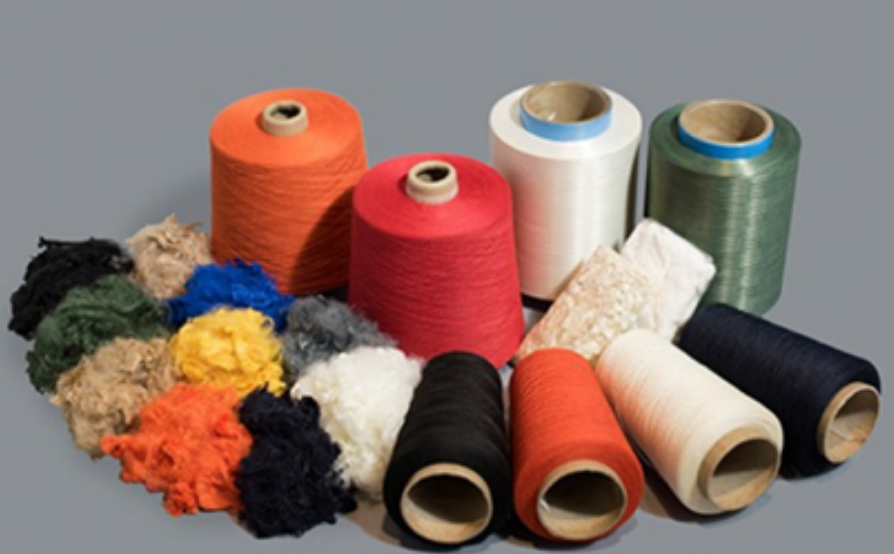
Aramid, first industrialized by DuPont in the 1960s, is a generic term for aromatic polyamides. Characterized by having over 85% of its amide bonds directly linked to benzene rings, forming long-chain synthetic polyamide materials, aramid comes in various types based on its structure, with meta-aramid and para-aramid being the most widely used. Meta-aramid is renowned for its excellent thermal stability, flame retardancy, and electrical insulation properties, while para-aramid is known for its high specific strength, high specific modulus, and high-temperature resistance, with a tensile strength six times that of steel wire.
According to the Color Masterbatch Industry Network, the global nominal capacity of aramid in 2024 was approximately 160,000 to 170,000 tons, with a demand of around 120,000 to 130,000 tons. China’s aramid capacity has surpassed 30% of the global total. In the global capacity landscape, DuPont ranks first, followed closely by Teijin, with Tayho Advanced Materials in third place. In terms of meta-aramid capacity, DuPont leads, followed by Tayho, with Teijin in third. For para-aramid capacity, DuPont remains atop, with Teijin in second and Tayho in third.
From a patent perspective, between 1960 and 2024, the global number of aramid patent applications reached 24,817, indicating that patent technologies have entered a mature stage. Against this backdrop, companies like DuPont and Teijin are actively responding to the challenges of intensifying market competition by optimizing products, enhancing efficiency, and exploring new technologies. In terms of patent technologies, DuPont focuses more on improving product comfort and wear resistance, while Teijin emphasizes enhancing flame retardancy and strength.