November 08, 2024 – Mastering the Matte: An Insight into Additives for Dull-Finish Plastics
In the plastics industry, achieving a matte finish has always been a pivotal aspect of product design. This effect, characterized by a non-glossy, soft visual appeal, hinges on the strategic use of various additives during the manufacturing process. Today, we delve deep into these additives and explore how they contribute to the desired matte finish in plastic products.
At the heart of creating a matte finish lies the disruption of the plastic’s surface smoothness, causing light to scatter rather than reflect in a concentrated manner. This is where matte-effect additives play a crucial role. Among them, matting agents stand out as the most vital. By diffusing light, these agents effectively prevent it from reflecting off the plastic surface uniformly, thereby reducing glossiness. Besides their matting capabilities, matting agents also conceal surface imperfections, enhance adhesion, and boost durability. Commonly used matting agents include calcium carbonate, talc, and silica, each with unique properties tailored for specific applications.
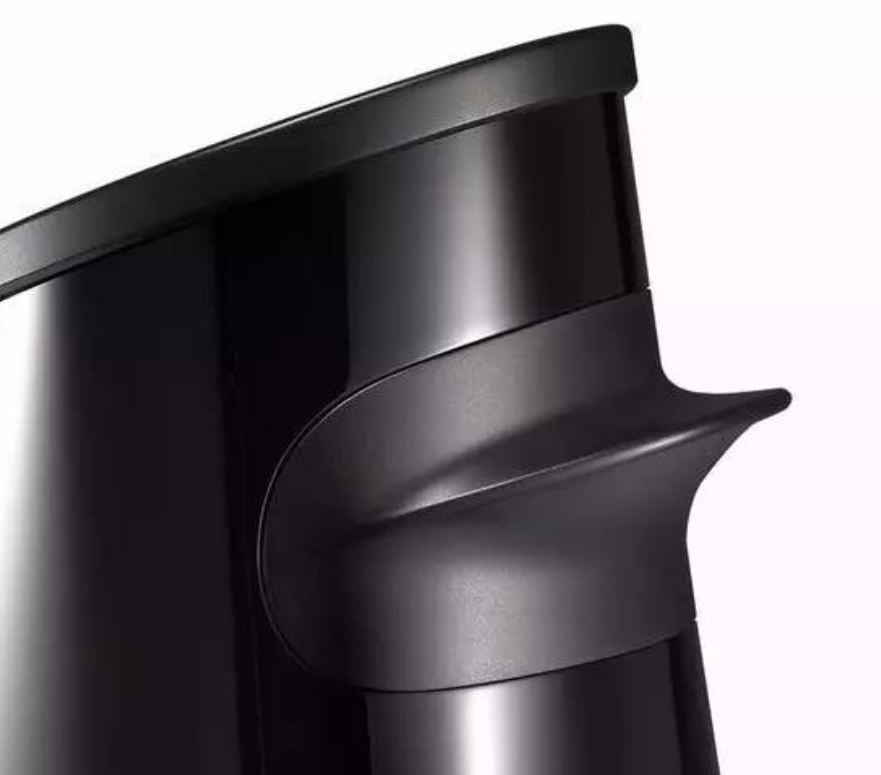
Plasticizers, another significant factor influencing plastic gloss, can also contribute to a matte finish. Certain plasticizers lower the processing temperature of plastics while simultaneously reducing their gloss, resulting in a duller surface. When combined with liquid plasticizers, solid plasticizers like nitrile rubber notably increase plastic flexibility and softness while improving surface texture to achieve a matte appearance.
Minerals such as alumina and magnesium oxide are widely used in plastic matte treatments, particularly for high-performance applications. They enhance plastic durability and scratch resistance. Wax additives, including polyethylene wax and paraffin, when used in conjunction with matting agents like silica, provide a more enduring matte finish.
Other additives in the plastic processing workflow also impact gloss levels. Pigments, for instance, not only impart color but also alter the plastic’s gloss to some extent. Antioxidants and UV stabilizers, used to prevent plastic degradation from oxidation and UV exposure, can also influence glossiness as a secondary effect.
Notably, specific plastic types like PVC and EVA have unique methods for achieving a matte finish. In PVC, selecting resins with higher K values and cross-linked resins can lower gloss. For EVA, adjusting the VA content and extrusion parameters when used in conjunction with PVC can effectively yield a matte effect.
In conclusion, achieving a matte finish in plastics requires a comprehensive consideration of various factors, including additive selection and processing condition optimization. As technology advances and the market evolves, more innovative additives and processing techniques are expected to emerge, bringing exciting possibilities and further enhancing the plastics industry’s capacity to deliver exceptional matte finishes.