April 24, 2025 – In a multitude of industrial applications, rubber products such as rotary shaft seals and automotive windshield wipers operate under dynamic sliding conditions. Reducing the friction coefficient of rubber surfaces is not only crucial for minimizing operational resistance but also plays a pivotal role in extending product lifespan and enhancing overall performance. To achieve this, the industry is delving deep into two primary research directions: surface chemical modification and physical coating.
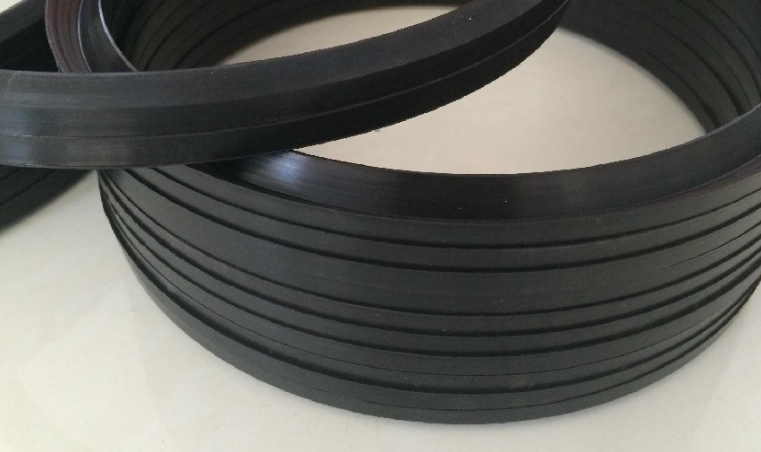
Surface chemical modification technology aims to reshape the properties of rubber surfaces through specific chemical reactions. This approach can precisely target the area ranging from 0.01 to 10 micrometers beneath the surface of vulcanized rubber. Complex chemical reactions, including substitution, displacement, and cyclization, are employed to alter the material’s surface structure. The type of treatment agent, treatment duration, and oxygen involvement all significantly influence the modification outcome, while the migration of modified substances determines the final structure of the surface layer. Experimental data indicates that after undergoing various chemical modification processes, the friction coefficient of rubber surfaces decreases remarkably, effectively boosting their wear resistance.
Physical coating, another key technological pathway, has witnessed significant breakthroughs in materials and processes. Take poly(p – xylylene) as an example. This material can form a transparent and elastic film via coating or vacuum deposition methods. With a friction coefficient of 0.25 – 0.33, which is comparable to that of PTFE dry films, it adheres closely to the rubber matrix and can withstand deformation. The deposition process involves evaporating the dimer at around 150°C, cracking the vapor into p – xylylene biradicals at 680°C, and then polymerizing these monomers onto the rubber surface in a room – temperature vacuum chamber. Lubricant film coating relies on solid lubricants like graphite and molybdenum disulfide. Through three processes—coating mixing, suspension treatment, and latex dispersion—this technique constructs a lubricating layer with a lamellar sliding structure on the rubber surface, transforming traditional stick – slip friction into intermolecular sliding and significantly reducing wear. Moreover, PTFE, with its excellent self – lubricating and weather – resistant properties, is an ideal coating material. Despite the challenge posed by its low surface energy, five innovative techniques, including radiation grafting and plasma activation, have successfully overcome the material bonding issue, greatly enhancing the wear resistance and medium resistance of rubber products.