May 20, 2025 – Driven by stringent environmental policies and evolving consumer preferences, the polyethylene (PE) white masterbatch industry is rapidly transitioning towards mid-to-high-end market segments. As a cornerstone material in plastic coloring, PE white masterbatch, celebrated for its exceptional whiteness, dispersibility, and functional attributes, finds extensive applications in premium sectors such as liquid packaging, cast coating, and multilayer co-extrusion. From AsiaMB’s specialized vantage point within the color masterbatch industry, this article delves into the application requirements of mid-to-high-end PE white masterbatch across various niche markets, aligning with the latest industry standards and technological advancements.
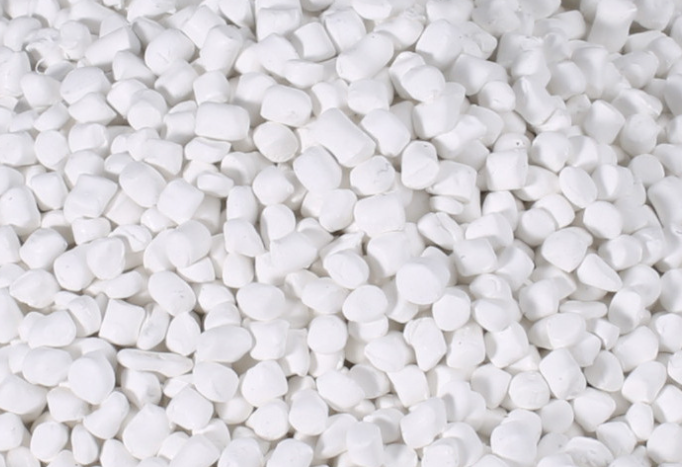
Polyolefin White Masterbatch (LDPE/LLDPE/HDPE)
Primarily utilized in supermarket shopping bags, gift packaging, clothing and hat packaging, liquid packaging, cast coating, and as the base color for multilayer co-extrusion films, polyethylene white masterbatch has witnessed a shift towards higher-grade products in response to national environmental regulations. This shift has led to the gradual phase-out of low-end, ultra-thin products, with a focus on mid-to-high-end white masterbatches tailored for blown film (co-extrusion), cast coating, and liquid food packaging applications.
- White Masterbatch for Liquid Packaging
- Primarily used in packaging for milk, sauces, vinegar, ham sausages, lactic acid beverages, and pharmaceuticals, these masterbatches must be non-toxic, heavy metal-free, free of extractables, fluorescent-free, odorless, and certified by health authorities. They should exhibit a glossy, uniform white appearance with even particle distribution and meet the QB1648-92 industry standards for polyethylene color masterbatches post-dispersion.
- Seals must be robust, withstanding a minimum air pressure of 200 kg/m².
- No yellowing or discoloration should occur, and the material must resist outdoor light exposure for at least six months.
- Melt flow rate should slightly exceed 3 g/10 min (190°C/2.16 kg).
- White Masterbatch for Cast-Coated Food Packaging Bags
- Requires a glossy, uniform white appearance with good dispersibility.
- Must withstand temperatures exceeding 300°C.
- Moisture content should not exceed 500 ppm.
- Peel strength must exceed 0.7 N/15 mm.
- Migration resistance should reach level 5 or higher.
- Melt flow rate should be controlled above 7 g/10 min (190°C/2.16 kg).
- Must be non-toxic, heavy metal-free, free of extractables, fluorescent-free, and certified by health authorities.
- No yellowing should occur, and the material must resist outdoor light exposure for at least six months.
- Should exhibit good crack resistance.
- High-End Packaging Bags for Multilayer Co-Extrusion, Gravure Printing, and Dry Lamination
- Must have a glossy, uniform white appearance with good dispersibility.
- Average particle size after dispersion should not exceed 0.4 μm.
- The film surface should be smooth, not affecting corona treatment, with a surface tension of at least 38 dynes/cm, testable with a dyne pen.
- Should be free of heavy metals, toxic substances, and extractables.
- Melt flow rate should be controlled between 2-3 g/10 min (190°C/2.16 kg).
- Should exhibit good resistance to yellowing, withstanding outdoor light exposure for at least six months.
- Should have good printability and adhesive properties.
- High-Temperature Sterilization Films
- In addition to food packaging film requirements, these films must demonstrate excellent oil resistance, seepage resistance, and solvent resistance.
- Melt flow rate should be controlled within 2 g/10 min (190°C/2.16 kg).
- Seals must be robust.
- CPP Cast Films
- Should have a rigid, glossy surface with good tear resistance and high-temperature resistance, not falling below 121°C/20 min.
- Must exhibit excellent oil resistance, seepage resistance, and solvent resistance.
- Melt flow rate should be controlled within 2 g/10 min (190°C/2.16 kg).
- Seals must be robust.