September 09, 2024 – The issue of color fading in plastic colored products has garnered widespread attention in the industry. The fading phenomenon is closely related to various factors, including the light resistance, oxidation resistance, heat resistance, and acid-alkali resistance of the color powder. Additionally, the characteristics of the resin used also play a crucial role. To delve deeper into this matter, here is a detailed analysis of the factors contributing to color fading in plastic colored products.
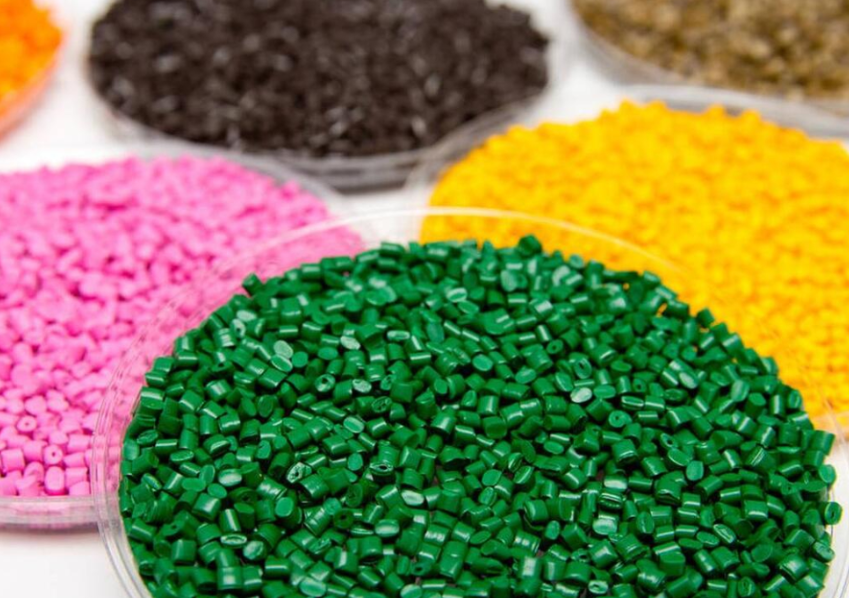
Firstly, light resistance is a key factor affecting the fading of colorants. For outdoor products that are often exposed to strong light, the light resistance level of the colorant is crucial. If the light resistance level is insufficient, the product will fade quickly, affecting its aesthetics and service life. Therefore, for weather-resistant products, colorants with a light resistance level of six or above should be selected, while for indoor products, levels four or five may suffice. Furthermore, the light resistance of the carrier resin also impacts color stability. Changes in the molecular structure of the resin caused by ultraviolet rays may lead to fading. Hence, adding light stabilizers such as UV absorbers to the masterbatch is an effective way to improve light resistance.
Secondly, heat resistance is another important consideration. The thermal stability of pigments during processing is directly related to their degree of discoloration and fading. Inorganic pigments usually have good heat resistance due to their stable composition. However, organic pigments may undergo molecular structural changes and decomposition at certain temperatures, especially in high-temperature processing environments such as PP, PA, PET, and other product processing temperatures that can reach above 280℃. Therefore, when selecting colorants, it is necessary to consider both the heat resistance and duration of the pigment.
Moreover, oxidation resistance cannot be ignored. Certain organic pigments may undergo degradation or other chemical changes after oxidation, leading to fading. This oxidation can occur in high-temperature environments during processing or be triggered by strong oxidizing agents. For example, when mixed with chrome yellow, lake and azo pigments may gradually fade in red color.
Lastly, acid-alkali resistance also significantly affects the color stability of colored plastic products. The chemical resistance of colorants, including acid-alkali resistance and redox resistance, is directly related to the fading of products. For instance, molybdenum chrome red is resistant to dilute acids but sensitive to alkalis, while cadmium yellow is not acid-resistant. These chemical properties may have a strong reducing effect when combined with specific resins such as phenolic resin, further affecting the stability and weather resistance of the colorant.
In summary, to address the fading issue in plastic colored products, it is essential to comprehensively consider the performance of required pigments, dyes, and various additives, including light resistance, heat resistance, oxidation resistance, and acid-alkali resistance. Through scientific selection and proportioning, the color stability and service life of plastic colored products can be effectively improved.