August 05, 2024 – PEEK (Polyetheretherketone), a high-performance thermoplastic engineering plastic, has garnered widespread adoption across various industries, including aerospace, automotive manufacturing, electrical, and medical devices, due to its exceptional mechanical properties, high temperature resistance, chemical stability, and outstanding electrical insulation capabilities. Let’s delve deeper into the remarkable performance characteristics of PEEK material.
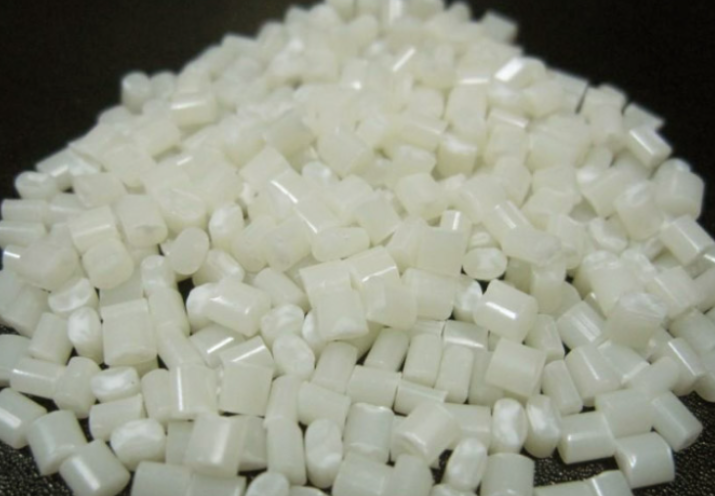
Notably, PEEK boasts a high melting point of approximately 343°C, enabling it to maintain exceptional dimensional stability in high-temperature environments. With a density of roughly 1.3 grams per cubic centimeter, its relatively lightweight nature contributes to reducing the overall weight of products. Remarkably, PEEK also exhibits superior flame retardancy, achieving a UL94 V-0 flame retardant rating without the need for any additional flame retardants.
In terms of mechanical properties and temperature resistance, PEEK demonstrates exceptional performance. It possesses high strength, rigidity, and outstanding impact resistance. Even at temperatures up to 250°C, PEEK retains its excellent mechanical properties, making it an ideal material choice for high-temperature applications.
Furthermore, PEEK exhibits exceptional chemical stability and corrosion resistance. It demonstrates robust resistance to various chemicals, including acids, alkalis, and organic solvents. This characteristic makes PEEK a preferred material for critical components in chemical processing and analytical equipment.
PEEK also excels in wear resistance and fatigue strength. Its outstanding wear resistance and dynamic fatigue strength make it stand out in industries requiring long-term durability, such as bearings, gears, and sealing applications.
In addition to these attributes, PEEK is an excellent electrical insulator. Its electrical properties remain stable even in humid environments or after prolonged exposure to gamma or X-rays. Therefore, PEEK finds extensive use in the manufacture of high-end cables and components.
According to AsiaMB, the processing performance of PEEK material is also remarkable, allowing for manufacturing through various methods such as injection molding and extrusion. This makes PEEK easy to fabricate into complex shapes and components. Due to its exceptional overall performance, PEEK is widely used in spacecraft structural components, automotive transmission systems, semiconductor manufacturing equipment, and artificial bone implants.
In conclusion, PEEK material plays an indispensable role in numerous industrial sectors, thanks to its unique performance parameters. Whether it’s stability under extreme temperatures or durability in complex chemical environments, PEEK fully demonstrates its value as a high-performance engineering plastic. As technology continues to advance, the application prospects for PEEK are poised to become even broader.