October 16, 2024 – Unraveling the Mystery of Color Variation in White Color Masterbatch and Its Solutions
The issue of color variation in white color masterbatch during application has garnered significant attention within the industry. To provide a deeper understanding and address this challenge, this article delves into the causes of color change in white color masterbatch and the corresponding solutions.
In the utilization of white color masterbatch, dilution is often necessary to minimize fiber color differences after coloring, with strict control over the mixing ratio. For filament yarns, the mixing ratio should not be less than 3% to 10%, while for staple fibers, it should be no less than 1% to 3%. When producing单色bulked continuous filament yarn, a three-color equipment setup is typically employed, ensuring that the white color masterbatch is fed into the extruder after mixing. To further enhance melt mixing capability, additional mixing devices are sometimes installed along the extruder section.
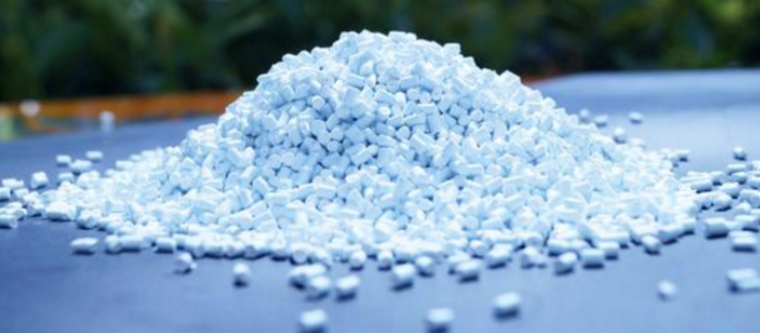
According to AsiaMB, the method of incorporating white color masterbatch becomes particularly crucial once the color formula for colored yarn is determined. Uniform dispersion of the white color masterbatch in polypropylene chips prior to spinning is a vital step in ensuring product quality. There are two primary mixing methods: the gravimetric and volumetric approaches. One effective method involves melting the white color masterbatch in or near the extruder and injecting it into the polypropylene melt through a smaller extruder, achieving excellent uniformity.
Selecting the appropriate white color masterbatch depends on the specific application. Polypropylene color masterbatches are categorized into fine denier and coarse denier grades, and coarse denier white color masterbatches cannot be used for coloring fine denier fibers. Therefore, when selecting colors, consideration must be given to the denier of the spun fiber, and the corresponding grade of white color masterbatch should be chosen. To maintain consistent product quality, it is advisable to use white color masterbatches from the same manufacturer and prioritize high-concentration products to reduce costs.
The quality of the pigments in white color masterbatches also plays a significant role in the quality of the finished fiber. Pigments are classified as high, medium, and low-grade, and different grades of white color masterbatches should be selected based on the quality requirements of the fiber being produced. Additionally, to prevent quality variations in the finished fiber due to differences in the light and thermal stability of the pigments, it is important to choose white color masterbatches that meet the fiber quality requirements and have the same level of light and thermal stability.
So, what causes white color masterbatch to change color? Possible reasons include changes in processing techniques, insufficient cleaning of the plastic machinery, inconsistent base colors of raw materials used, uncleaned feeding gates, improper mixing of water port materials, color differences in the color masterbatch or color powder itself, low temperature resistance of the color masterbatch or color powder used, and uncleaned or improperly controlled mixing times in the mixer.
To address these issues, the following solutions can be adopted: use raw materials consistent with the color used during the color matching process and adjust the mixing ratio of water port materials; thoroughly clean the plastic machinery, feeding gates, and mixers; switch to color masterbatches or color powders with appropriate temperature resistance and consistent color; and use stable processing techniques. By implementing these measures, the problem of color variation in white color masterbatch during application can be effectively avoided, ensuring product quality and stability.