March 17, 2025 – Europe’s chemical industry is undergoing a dramatic contraction, with the European Chemical Industry Council reporting the shutdown of approximately 11 million tons of annual production capacity between 2023 and 2024. Olefins capacity has been reduced by 26%, resulting in a loss of 2.86 million tons of ethylene and propylene output. According to BASF CEO Markus Kamieth, the company’s strategic pivot—including the expansion of its integrated site in Zhanjiang, China—is a direct response to Europe’s economic stagnation, uncertain U.S. tariff policies, and intensifying regional competition.
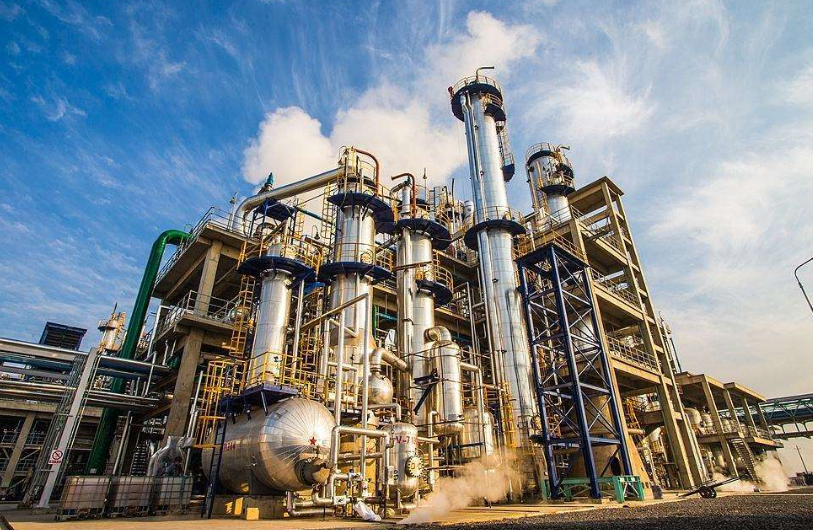
The dual pressures of soaring energy costs and tightening environmental regulations have accelerated this industrial retrenchment. The Russia-Ukraine conflict triggered a spike in natural gas prices, forcing BASF to idle or scale back ammonia and adipic acid facilities at its Ludwigshafen hub due to surging syngas expenses. With the EU’s Carbon Border Adjustment Mechanism (CBAM) set to take effect in 2026, the industry now faces additional carbon costs of tens of euros per ton. Consequently, giants like INEOS and Dow are slashing European operations and refocusing on high-value sectors such as healthcare and specialty chemicals.
China, meanwhile, has emerged as a magnet for global chemical investment. Data from Germany’s Chemical Industry Association reveals that nearly 20% of German chemical investments have redirected to China, with BASF’s Zhanjiang site—a €10 billion project—poised to establish a full-chain production ecosystem upon its 2025 completion. Professor Lin Boqiang of Xiamen University attributes this shift to China’s vast consumer market, cost advantages, mature industrial clusters, and preferential policies like tax incentives. Despite China’s chemical industry profitability plunging to a record-low 4.5% in 2024, insiders argue that foreign capital inflows will catalyze domestic technological upgrades, driving the sector toward premium and sustainable models through knowledge spillovers and joint ventures.
Notably, BASF’s Zhanjiang facility exemplifies this green transformation, achieving 30% lower carbon emissions than European standards for its acrylonitrile plant and recycling 95% of wastewater. Such eco-friendly manufacturing capabilities may solidify China’s competitive edge in absorbing global capacity relocations. As 2025 accelerates the reconfiguration of global chemical supply-demand dynamics, the synergy between Chinese and international firms amid competition will define the industry’s future trajectory.